走进广东佛山三水的奥瑞金佛山工厂大门,可直线通往生产车间,越走越近,三条生产线运转的轰隆声开始震动你的耳膜。这里是奥瑞金产能最大的两片罐工厂,年产能可达26亿罐;这里也是百威亚太最大的单个供应厂,承接了百威330#罐持续减重的项目,生产出重9.57g、堪称“国内最轻”的减重罐。
车间门口挂着的一行字格外引人注目:“目标(Target): Global VPO EP No.1。”
奥瑞金2021年正式加入百威战略合作供应商联盟(SSA)项目,在企业管理领域深化合作,佛山工厂2021年和2022年连续获得百威战略合作供应商联盟最重要奖项——“最佳供应商奖”,他们第三年的目标是做到VPO项目的“全球第一”。
无论最轻还是最佳,都不容易。VPO在佛山工厂的故事,是一个要求在管理和制造等细节上精益求精的过程。
自 2021 年推行 VPO 项目以来,奥瑞金佛山工厂在轻量化方面成绩斐然,9.57g 的 330# 罐实现国内最轻,未来计划减重至 9.30g。
“把中国制造业水平往上提,这是一个伟大的想法”
英语缩写似乎有一种魔力,越简单到只有两三个首字母,越让人感觉神秘。从门口的那一个“大标题”开始,走入奥瑞金佛山工厂,无论在办公区域的展示板还是厂间工作站,随处可见“VPO”。
VPO为工厂最优化管理Voyager Plant Optimization的缩写,是百威英博总部在全球各子公司广泛推行的有效管理工具。百威利用全球250家酿造厂网络,每月用超过30个KPI指标,来对比检测公司在亚太各地酿造厂的生产率、啤酒质量与口味等。EP则是百威最佳供应商的评比项目Excellent Program(卓越项目)。2021年奥瑞金佛山工厂开始推行百威VPO项目,以提升安全水平、建立更可靠的维护系统,降低故障率、提升员工技能和能力、提高效率和减少质量损失等。
“奥瑞金收购佛山工厂后,以及加入百威战略合作供应商联盟(SSA)三年以来,我们可以切身感受到各方面的进步。”奥瑞金(佛山)包装有限公司总经理李颖杰说,“VPO带来的帮助,比我们此前预想的要多。”
李颖杰加入佛山工厂之初,曾到国外进行行业培训学习,“从原材料、流程管理、设备维护、人员配置、客户审核等方方面面体验下来,我能感受到,国外工厂非常擅长数据分析,利用精细化数据推导,他们非常注重将流程标准化,这样有利于传承,使后来者能快速完成摸索熟悉这一过程。”
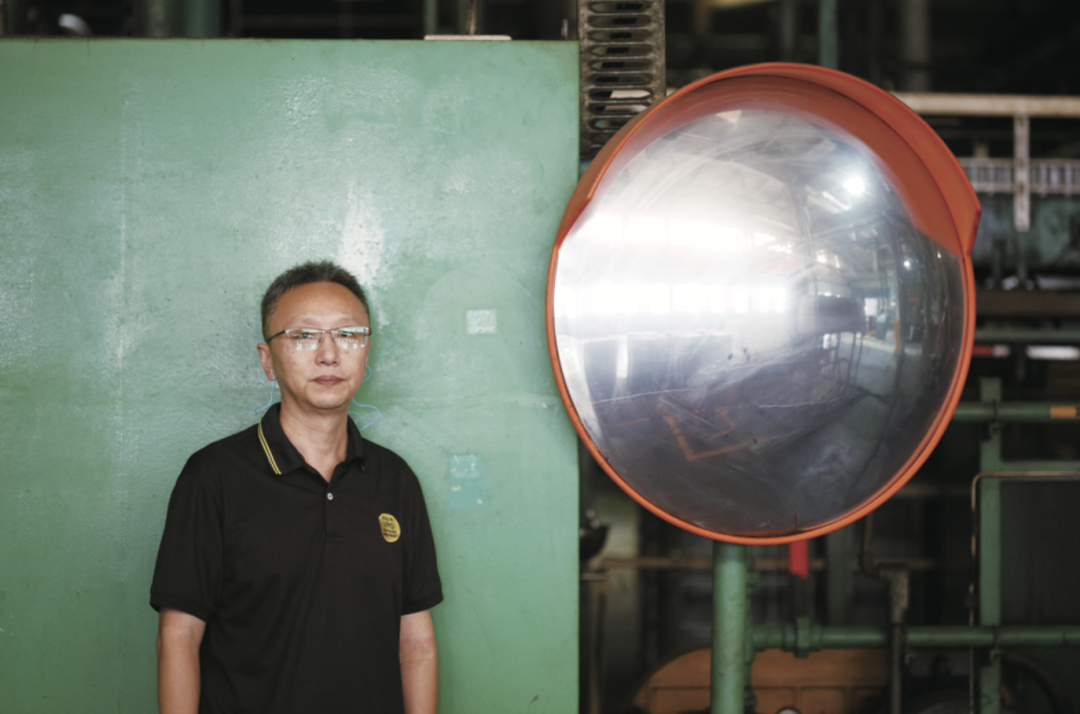
陈环慧 · 奥瑞金佛山工厂人事行政经理
VPO项目在佛山工厂的推广,正是一套精细化管理体系的融合之路。李颖杰分享说,百威派遣专人前来佛山工厂指导、开展各类培训,以及邀请到其他工厂参观学习,让佛山工厂的VPO推行之路快速实行,“百威非常开诚布公地分享他们的方法经验,比如在能耗方面,奥瑞金佛山工厂积极践行可持续发展战略,通过中水回用,每天能节省用水三四十吨。这是百威给我们带来的好建议的一例。”
“百威在推动的事情,能把中国制造业水平往上提,这是一个伟大的想法。”
作为百威亚太最大的供罐商,奥瑞金两片罐已有8家工厂为百威供罐,佛山工厂是推行VPO的优秀模范。今年,百威在EP项目推动中国供应厂商与国外百威的工厂进行对标,佛山工厂作为中国四家供应商工厂代表之一,目前是唯一一家参加PK的易拉罐工厂。
李颖杰说:“这是我们为什么在门口挂那一行字的原因。百威在中国的world calss(世界级)工厂已经有约十家,我们是中国供应商参与百威VOP竞争的唯一种子选手,(参加PK)有压力,也是一种实力得到认可的荣幸与动力。”
2021年百威于佛山工厂VPO启动的目标,包括2021佛山百威DMR(Defective Material Report,材料缺陷报告)比2020年降低50%、罐子质量问题导致百威停机时间为“0”、节约成本的目标等。降低DMR,特别是在百威审核要求非常严格的情况下做到提高,是非常具有挑战性的,但李颖杰说:“我们成功做到了DMR的持续改善。DMR由2021年17单,到目前为止,只有1次的DMR。这就是我们交出的成绩单。”
佛山工厂车间里挂着那条“我们是最优秀的制罐团队”的横幅,不是纯粹心理暗示,而是自信。百威SSA基本囊括了国内所有的优质供应商,包括宝钢、中粮、昇兴等,能脱颖而出绝非易事。
“每上一个台阶,需要一年时间”
佩戴护耳器进入佛山工厂车间,能隔绝大部分机器噪音,此时有规律的金属碰撞声,扑面而来的热浪,明暗交错的光线,让机器构筑的钢铁森林有了别样生命力。
这里已经是一个有三十年历史的老厂,第一眼望过去,自然不会有光鲜亮丽的惊艳感,甚至有些暗。这是因为车间里并没有打开全部灯,而是保障一些必需位置的照明,这是佛山工厂积极推动合作商百威可持续发展战略的做法。2022年,百威开始帮助供应商们建立碳排放的基准,将节能减排和新能源引入到整个过程中(更多内容可见2023年第二期《奥瑞金人》对百威亚太的相关采访)。
李颖杰介绍说,原本佛山工厂有四条生产线,其中一条已经搬到江门工厂,而那里的工厂自然比这里更加现代,“佛山工厂规划中的新厂一旦落成,太阳能光伏发电等新能源应用也都会有全面的提升”。
广东人有句俗话说,“禾秆盖珍珠”,越不显山露水,越有脚踏实地的实力。百威、健力宝、可口可乐、百事可乐、青岛啤酒、雪花啤酒、燕京啤酒、天地壹号、屈臣氏,等等,市面上最常见的饮料品牌,都能在这里找到它们正在生产的易拉罐。
佛山工厂生产国内最轻的330#罐,在百威 2022 VPO 论坛会议创新专题会——ISA(创新战略联盟)环节,奥瑞金这款仅重9.57g的减重罐获得极大关注,并捧回了 ISA大奖“突出贡献奖”。
这一个“最”并不包含多大的技术秘密,但却代表了引领中国金属包装行业“轻量化”的趋势。奥瑞金多年来一直在为罐“减重”积极探索,而在“双碳”政策目标之下,减重更将成为一个金属包装企业基本的技术要求。
李颖杰介绍说:“减重是可持续发展的需求。一只罐的重量变少,意味着消耗的铝材更少,更节能。欧洲已经做到白罐9.4g左右,而我们厂目前是9.57g,相比之前的9.76g还有更往前的9.8g,已经完成几次进步。”
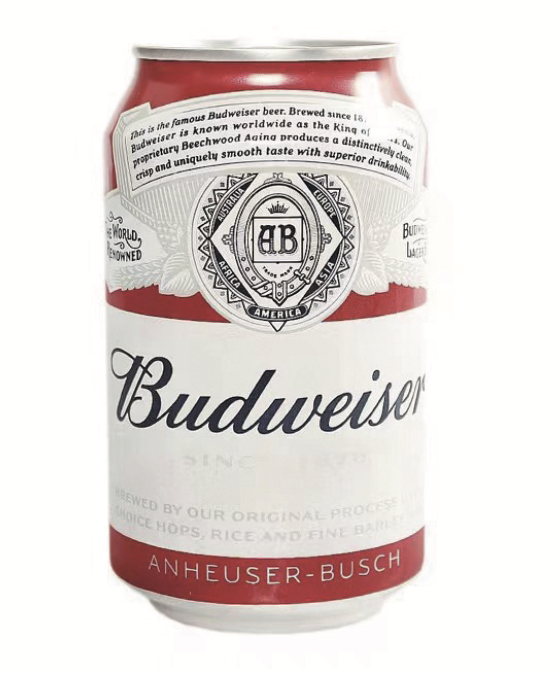
佛山工厂为百威实现的国内最轻 330# 罐, 重量仅为 9.57g。
“我们每上一个台阶,都几乎需要一年时间。”李颖杰说,每减重一步,都涉及模具设备的调试阶段,也要确保产品能符合轴压、耐压等方面的技术指标。佛山工厂目前已经具备将罐重降到9.45g的能力,只需等百威将新的CDL盖型定下,便能立即开启更轻时代,“我们和百威未来的目标是9.30g”。
一只罐的瘦身减重过程,意味着所有的加工流程要更加严谨。罐身减薄,意味着铝材在拉伸变薄过程中更容易出现拉断,断罐率的控制相比之前变得困难。奥瑞金佛山工厂近几年来一直着力降低断罐率,同时要兼顾几条生产线不同罐型的切换要求,也要保证设备能持续稳定运行。目前,佛山工厂的标准罐断罐率平均保持在20次/百万个以内,纤体罐断罐率在15次/百万个以内,已经低于奥瑞金集团给出的不高于21次/百万个的断罐率指标。
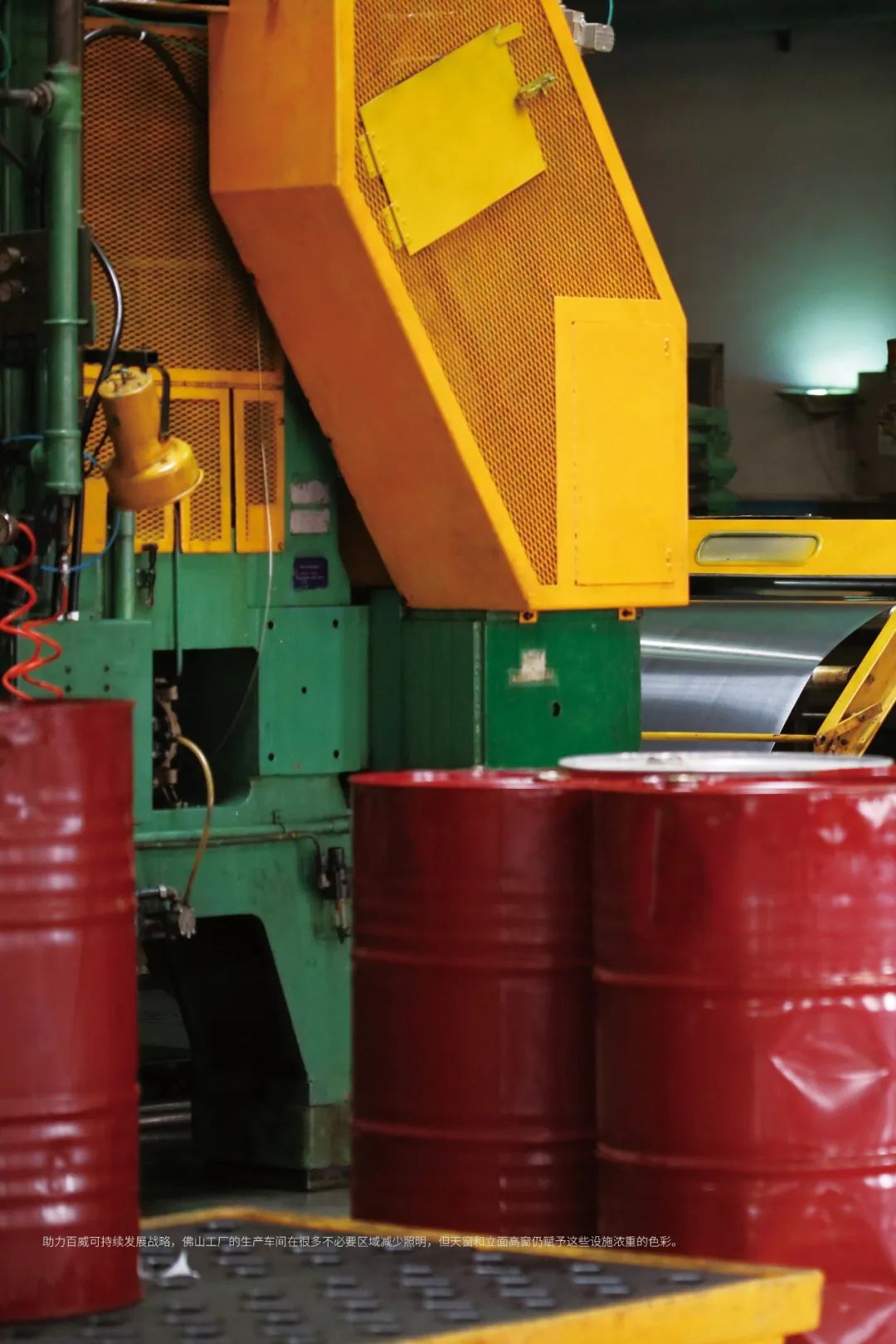
助力百威可持续发展战略,佛山工厂的生产车间在很多不必要区域减少照明,但天窗和立面高窗仍赋予这些设施浓重的色彩。
市场也在逼迫企业进行优化。李颖杰回顾,从2016年开始,中国的易拉罐市场就全面“卷”了起来,进入供过于求的局面,“中国的易拉罐年产量明年将达到800亿罐左右,而市场需求在500亿至600亿罐之间。在生产上,大家几乎没有技术秘密可言。而面对饱和市场,一条路是走低价路线,目前中国已经做到全世界最低价;另一条路则是减耗增效、提升员工能力。”
作为金属包装头部企业,奥瑞金在积极推动中国相关绿色材料运用上,已经达到了国际先进水平。铝材是易拉罐制造占比最重的成本项,减重将带来材料和能耗上的节约。“比如同样一吨铝材,以前理论上能制造约8万6千只罐,变薄变轻之后,理论上能制造8万8千只罐。”李颖杰说。
减重罐的生产,是创新与环保的需求,这不仅关乎流程上模具、设备参数等硬件的调整,更需在管理体系上步步升级,所有的一切都要围绕指标提升去设计。奥瑞金与百威合作推行VPO,也是不谋而合。
“我们要讲同一种语言”
佛山工厂诞生时是带着时代弄潮儿属性的。
上个纪90年代开始,包装(易拉罐、塑料瓶、纸箱)便已开始成为三水当地的新型工业体系之一。这其中不得不提一个曾红极一时的品牌——健力宝。
1984年洛杉矶奥运会,从许海峰射下中国第一枚奥运金牌开始,中国代表团连续夺下15金8银9铜共计32枚奖牌。捷报频传,振奋改革开放后的国人,也让押注体育营销的健力宝一夜成名。
设计之初,健力宝便选择了当时国内少见的易拉罐进行包装,三水县农机三厂也先后从意大利和美国引入生产线,成立了广东饮料容器制造公司。到1992年,健力宝饮料厂将其收购作为配套,与香港富特波尔容器合资兴办健力宝富特容器公司,在如今的厂址上兴建当时亚洲最大的易拉罐制造厂。这便是今日奥瑞金佛山工厂的前身。
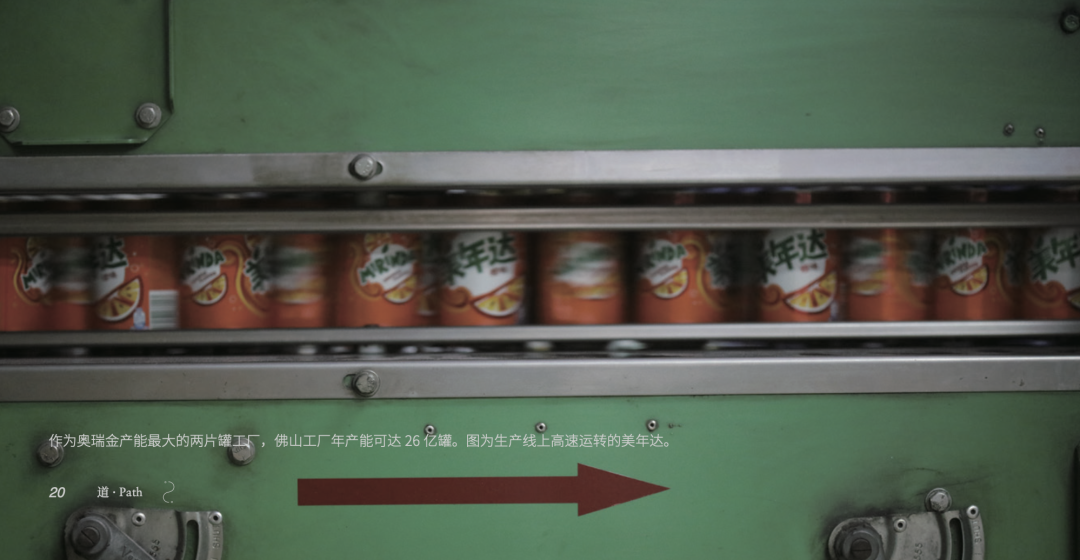
2010年,波尔亚太全资收购健力宝股份,之后公司更名为:波尔亚太(佛山)金属容器有限公司。从那时起,百威就已经是佛山工厂的最大客户。2019年,奥瑞金完成收购波尔亚太中国区业务,顺利延续与百威的合作,而佛山工厂也保持着国内两片罐最具竞争力的制造工厂水准。
奥瑞金佛山工厂人事行政经理陈环慧,自1993年大学毕业后入职以来,已见证了工厂三十年变迁。最初地处三水郊野的工厂,逐渐被城市包围,周围立起了高楼大厦。最近三年,陈环慧负责VPO人力支柱的推行工作,他将大家的心路历程比喻为一个人的求学之路:“一年级的时候还比较抗拒,不知不觉却已经开始接受,作为三年级的学生,我们感觉已经离不开VPO。”
对VPO,一线员工最初是有排斥反应的。
不难理解,没有什么体系能无缝衔接,特别是来自不同文化背景的管理体系。导入VPO最初最直接的一项,所有人的直观感受,便是在原来的工作任务上增加了新的工作量,特别是很多文件性的事项。这更需要管理上的磨合调整。
“我们要将原有的东西系统化,慢慢转变结合为百威VPO模式,毕竟万变不离其宗,很多工作内容是相类似的。”陈环慧举例说,梳理认可机制,集中为一个系统,每月定期评选各个认可奖项,同时将认可审批流程简化,使获奖员工有当选即领奖的快感。虽然只有象征性的一两百元奖金,但奖轻荣誉重,“就像考试拿了全班第一的那种感觉”。
除了在薪酬和考核上给予员工更多了解VPO的动力,佛山工厂还设立“VPO知识问答”环节,将培训寓教于乐,在员工饭堂设置有奖扫码答题,以纸巾牙膏沐浴露等日常生活小用品作奖品,让VPO的基础理念无声润入所有人的生活之中。
陈环慧的工作服上面有一个“VPO持续改善”的标志,“供应商跟客户要讲同一种语言,试想一下,如果一个人说英语、一个人说普通话、一个人说客家话,那大家一起就很难沟通到位。在我看来,VPO的关键便是不断发现问题并抓住改善机会点,当我们逐渐了解并接受它之后,便慢慢感觉得到它的反馈和帮助了”。
佛山工厂与百威的沟通频率变得更密集,管理、质量、人力、维护以及安全支柱等五大支柱的支柱长(部门经理)都参与其中,从安全、质量、产品和VPO的推进,涉及方方面面,“从最开始的半年审计,到每月的会议,如今则是双周会,与百威的沟通,帮助我们逐步改进更多问题,推动我们不断提升”。
“没有结果的VPO不叫VPO”
“没有结果的VPO不叫VPO。”奥瑞金佛山工厂厂长谭治兵这句话,是VPO在执行流程上的硬要求。
作为一位制罐行业的老行家,谭治兵2015年从国企离职后加入奥瑞金,2021年从陕西工厂来到佛山工厂,那年正好也是佛山工厂与百威协力推进VPO管理体系的开始。作为VPO项目支持,他对这套体系的感受主要来自两个方面:梳理了系统逻辑思维,发现问题解决到底。
“VPO要求的事情,我们以前也都有在做,但它作为一个体系,帮我们理清了很多思路。规范之后,做事情反而轻松多了,从管理层到员工,对所有事情都很清晰。”谭治兵说。
天下大事必作于细,天下难事必作于易。
对细节完美的执着,是很多成功企业的特性,麦当劳创始人克洛克曾说:“我强调细节的重要性。如果你想经营出色,就必须使每一项最基本的工作都尽善尽美。”松下创始人松下幸之助也说过:“不放过细节。无视细节的企业,它的发展必定在粗糙的砾石中停滞。”
何谓细节?简而言之,要有具体的内容,执行到位程度,让每个岗位都迅速明白自己的责权所在。佛山工厂生产线工作站上,整齐排列着各种表格,从标准、分工、责任到反应方案,指标细致到每一个步骤。
今年,佛山工厂正在推进设备维护的ATO系统(全员自主运行),为厂间设备维护、保养、清洁、润滑、检查、故障反应等环节建立一套新体系,谭治兵说:“其实它是在建立一种工作习惯,同时也提升员工的工作技能。”
“VPO对员工的要求,是你到达什么岗位,便能快速了解到岗位的关键控制点。因为指标已经被分解为各个岗位的小目标,无论大目标还是小目标,从产量到废品率、产品标准等,都有相应数据一目了然。”
“以前我们在工作中对各种要求也是一再强调、不断培训,内容都是差不多的。实行VPO之后又继续细致分解为各种流程指标,每个人每天到岗之后,都能知道自己需要完成的工作有哪些。”
对细节的认真把控,对质量的严格要求,也是奥瑞金一直秉承的匠人精神。来自百威的各种标注英文图表模块,与挂在生产厂间的一条横幅,一起描述他们对精益求精的追求:“以敬畏之心对待质量。”
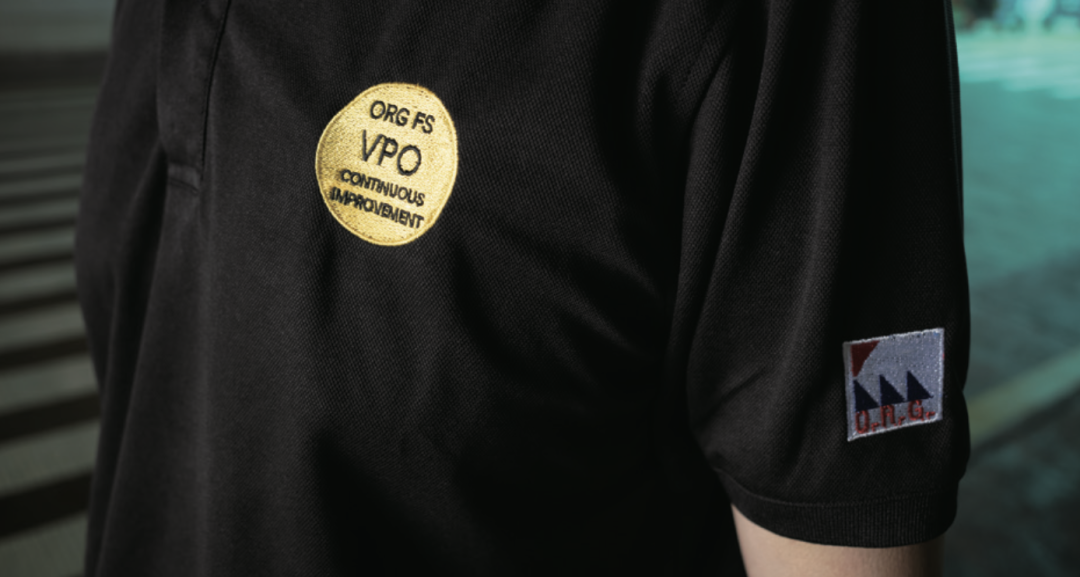
佛山工厂一位管理人员的着装,上有奥瑞金的 logo 和 VPO 的标志。
“一定要问5个Why”
类似的横幅与标语,提示着每一个岗位的员工对任何事情不可掉以轻心。
“控制每一道工序,做好每一件产品。”“发展决不能以牺牲人的生命为代价。”百威在佛山工厂启动的VPO项目包含了安全支柱、环境支柱、质量支柱、管理支柱、人力支柱、维护支柱以及物流支柱七大支柱,各个支柱再分解相应模块,每个支柱或模块的目标分数、标准指数、月度指标等,都清楚标注在每一个工作区域的展板上。
两片罐的产能主要看前端段,负责前端段设备维护的设备动力部负责人曾德,从2011年起便在佛山工厂工作,他记得2012年曾发生过一起冲杯机设备故障事故,导致生产线停机一周检修,最终判定问题出在涡轮,“但当时没有继续深入追溯故障发生的原因,结果2017年类似的问题再次发生。这一次不得不请专家前来分析,才找到真正原因”。
“在VPO推行之后,我们对设备的维护从技术上的思考,到思维上有所转变,考虑问题会变得更加开放,会从纵向横向进行对比,无论是工厂内的KPI,或是对比其他工厂。每当发现有问题的地方,一定遵循五个why(为什么),逐层逐层搞清楚,而且要求每一步必须可监控、可更换。”曾德说,“以前发生的那种故障,至今再没有发生过。”
为什么是五个“为什么”?问哪五个问题就能得到答案?
其实,这个VPO语言与中文里的“三”一样,有数量泛指的含义,事实上并不是死板要求问五个问题,而是指解决问题的方式必须层层追问,直至明确确认原因,排除故障发生的可能。这是VPO在生产线上的明确要求,讲究的便是打破砂锅问到底的精神,让每一处流程细节责任到位。
厂长谭治兵介绍说:“每个岗位上都有一个申报二维码。一旦故障或隐患发生,在岗员工即便能当场自主解决,同时要将问题和解决方案填写申报,这也是为后来人提供快速解决经验。这在指标上也有相应的整改率。”
“在员工赋能方面,奥瑞金一直做得不错。一定要让员工了解应该做什么,为什么这么做。一旦有问题解决不了,发现后一定要问五个why,如果层层反映仍解决不了,厂里便会成立攻关小组,必定要将问题解决到底。”
没有“差不多”这个选项,想要持续接近完善,持续发问就是最佳的方式,因为你经历过对问题的思考和对答案的追寻。乔布斯有句名言:“Stay Hungry,Stay Foolish。”保持持续学习的能力,是前进的基本动力。全心参与,持续改善,于每一处小细节保持学习和持续提高,最终回望便能感受到效率的提升。VPO与奥瑞金佛山工厂还在融合,每一处都跃动着新的刺激带来的活力。
$奥瑞金(SZ002701)$
本文作者可以追加内容哦 !