精益思维,源自丰田生产方式,强调“消除浪费,创造价值”。在PCB设计中,这意味着通过优化流程、减少冗余、提高自动化水平等手段,实现设计周期缩短、成本降低、质量提升的目标。精益思维不仅关注最终产品的品质,更重视整个设计过程的持续优化和效率提升。具体步骤如天行健精益生产顾问下文所述:
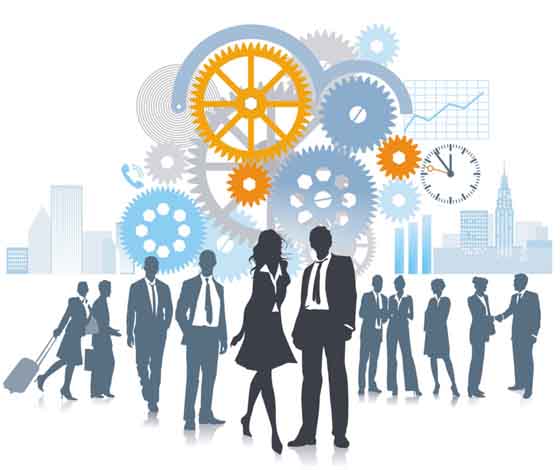
1、流程优化与标准化
消除非增值环节:精益思维首先要求识别并消除设计过程中的非增值环节,如不必要的评审会议、重复的数据输入等。通过引入自动化工具和标准化流程,如CAD(计算机辅助设计)与CAM(计算机辅助制造)系统的集成,可以大幅减少手工操作,提高设计效率。
标准化设计模板:建立标准化的设计模板和库,使得常用元件和电路布局得以快速复用,减少重复设计时间,同时保证设计的一致性和可靠性。
2、质量控制的精益化
预防性质量控制:在设计初期就融入质量控制的理念,通过DFM(可制造性设计)和DFA(可装配性设计)分析,提前发现并解决潜在的质量问题,避免后续生产中的返工和浪费。
自动化检测:采用先进的自动光学检测(AOI)技术,对PCB设计进行快速、准确的检测,确保设计的每一个细节都符合质量要求。
3、客户需求导向的设计
快速响应市场变化:精益思维强调以客户为中心,通过灵活的设计流程和快速迭代机制,快速响应市场变化和客户需求,缩短产品上市时间。
模块化设计:采用模块化设计思路,将PCB划分为多个功能模块,便于根据不同客户的需求进行快速组合和调整,提高设计的灵活性和可重用性。
4、绿色设计与可持续发展
环保材料选择:在PCB设计中优先选择环保材料,如低毒、可回收的基板材料,减少对环境的影响。
节能减排工艺:结合精益制造理念,优化PCB生产工艺,减少能耗和排放,实现绿色生产。
精益思维在PCB设计中的应用,不仅是技术层面的革新,更是管理理念和生产模式的深刻变革。通过不断优化设计流程、提升质量控制水平、快速响应市场变化以及实现绿色生产,企业可以在激烈的市场竞争中保持领先地位,为电子行业的持续发展贡献力量。
本文作者可以追加内容哦 !