在传统观念中,产品缺陷往往被视为失败的象征,是企业不愿面对也不愿提及的痛点。然而,在精益生产的视角下,缺陷不仅仅是问题的表现,更是隐藏着改进机遇的宝贵资源。每一个缺陷都是一次深入了解生产流程、识别浪费环节、激发创新思维的机会。因此,企业应当转变态度,将缺陷视为改进的起点,而非终点。具体步骤如天行健精益生产顾问下文所述:
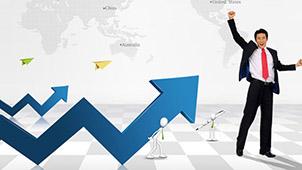
1. 全面记录与分析
首先,企业需要建立完善的缺陷记录机制,确保每一道生产工序中发现的缺陷都能被准确、及时地记录下来。这包括但不限于产品外观瑕疵、性能不达标、客户投诉等问题。随后,通过数据分析工具,对缺陷进行分类、统计和原因分析。这一过程有助于企业清晰地认识到问题的分布规律和根源所在,为后续制定改进措施提供有力支持。
2. 深度剖析根源
在了解了缺陷的基本情况后,企业需要进一步深入挖掘其背后的深层次原因。这往往涉及到生产流程、设备状态、员工技能、原材料质量等多个方面。通过采用“5Why”分析法(即连续追问五个为什么)或其他根因分析工具,企业可以逐步揭开问题的层层面纱,直至找到最根本的原因。这一过程虽然充满挑战,但正是它帮助企业避免了“头痛医头、脚痛医脚”的片面解决方案,确保了改进措施的有效性和长远性。
3. 制定并实施改进措施
基于上述分析,企业应针对性地制定改进措施。这些措施可能包括优化生产流程、升级设备设施、加强员工培训、改善原材料供应链等。重要的是,改进措施必须具体、可行且具有可操作性,能够直接针对问题根源进行改进。同时,企业还需要建立有效的监督机制,确保改进措施得到有效执行,并对实施效果进行持续跟踪和评估。通过不断试错、调整和优化,最终实现缺陷率的显著降低和生产效率的显著提升。
“从缺陷中挖掘机会”是精益生产项目选题的重要原则之一。它要求企业以开放的心态面对缺陷,将其视为宝贵的改进资源;通过全面记录与分析、深度剖析根源、制定并实施改进措施等步骤,不断挖掘生产流程中的潜在价值;最终实现生产效率的提升、产品质量的优化和企业竞争力的增强。
本文作者可以追加内容哦 !