现代汽车是车轮上的数据中心——智能联网并装满了传感器、智能软件和电子设备。在中高档汽车中,有时会有 100 多个控制单元处理大量数据,从而确保驾驶员从与安全、舒适和多媒体相关的各种功能中获益。这些功能包括距离或紧急制动辅助装置等辅助功能,也包括安全气囊和安全带张紧器等救生装置。因此,需要车规级线束产品来快速可靠地传输能量、信号和信息。
现代汽车中安装的电缆长达数公里。电缆的高效生产是供应商的决定性竞争因素。均普智能(PIA)开发了一种基于伺服凸轮平台的车规级柔性线束装配(KGM) 的解决方案,可全自动装配生产线束,其特点是模块化和可扩展的 KGM 不仅可以装配纯单芯或多芯线束,还可以根据客户要求装配连接件和组件。KGM 可以定制,组成不同形式的工位布局:PIA可以集成所有必要的工序,例如定长切线和剥皮,甚至是复杂的焊接工序。这为客户大批量生产高质量的线束提供了高效可靠的解决方案,代替以前耗时的手工工序,从而实现了完全自动化,且质量始终如一。
“这项技术(KGM)对机械设计有着较高的要求,是均普智能安贝格公司研发的行业领先性技术。”均普智能中国区CTO何川博士介绍,基于KGM的全自动线束装配,技术工艺复杂,但装配节拍很快,线束信号传输速度可以降到1秒以内,且稳定性非常好;而传统的线束生产工艺,通常信号传输速度都在1秒以上。 “这对于汽车安全系统来说至关重要。”
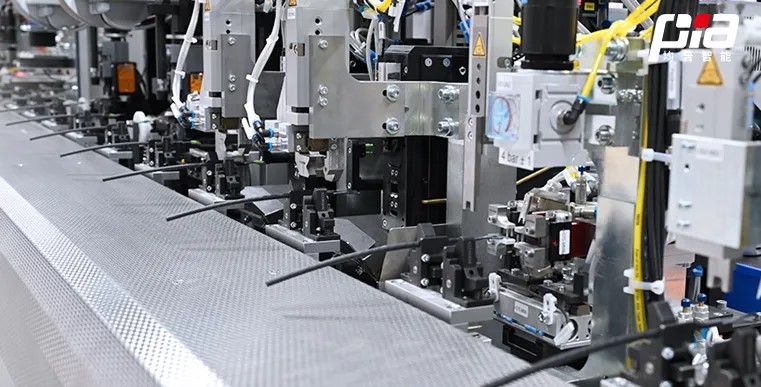
线束信号传输速度,决定汽车安全程度
组件和连接部件之间的有线信号传输在汽车被动安全系统中发挥着特别重要的作用。执行器用于触发安全气囊或 “主动引擎盖”:例如,在与行人发生碰撞时,执行器可在几毫秒内将引擎盖升起几厘米,这成为了一个额外的缓冲区来缓冲撞击。
信号必须以最快的速度发出,汽车被动安全系统才能更好地保护生命安全。因此,均普智能的客户对线束组件自动化生产的要求特别高。一位来自供应商行业的客户也是如此,他希望均普智能帮助其生产由线束和执行器组成的组件。在此之前,这一过程主要由手工完成。
“除其他要求外,客户还要求始终如一的卓越质量、集成到工艺流程中的检测过程以及以高速节拍实现装配流程。"均普智能销售团队协调员Herbert Knorr解释说。均普智能的专家们设计了一个基于KGM的系统,实现了所有工艺步骤的自动化:线束被送入系统后,首先被贴上标签、按长度切割,然后被剥皮和解捻。随后是进一步的装配流程,例如压接,通过塑性变形将各个部件连接在一起。在系统的第二部分,KGM 采用类似的工艺步骤对线束另一端进行最后的加工。该项目的一个特殊挑战是不同材料间的焊接。$均普智能(SH688306)$与客户和德国一所大学密切合作,开发出一种创新工艺,可将两种材料的组件可靠地焊接在一起。
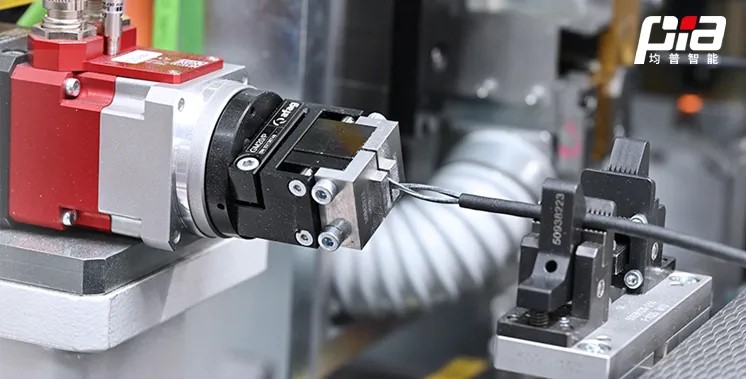
3.5秒一个新组件,可120小时连续生产电缆
该系统利用视觉组件,在装配过程中检测装配质量。一旦完成所有子步骤,生产线就会将完成的组件输出到小型装载工装中进行进一步加工。每根线束在装配完成后都可以实现装配流程的追溯,且过程中的所有相关数据都会被记录下来。这不仅是满足客户的要求,而且对于车辆安全系统尤为重要。还能实现高速节拍要求:每 3.5 秒就有一个全新的组件落入小型装载工装。
与此同时,该系统可以在客户的厂房内每周五天、每天 24 小时可靠运行。客户对 PIA 的线束装配系统非常满意。“我们的理念在该客户那里也得到了验证。“Knorr说,“该生产线能够可靠而经济地生产具有高度复杂连接设计的线束。”过去依赖大量手工劳动进行装配的员工,现在可以无忧地进行工作,因为装配工作已经实现了自动化,同时产品质量始终保持高水平。至于这些线束最终是用于电动汽车还是内燃机,与装配工艺无关。“我们的优势在于能够适应客户的不同要求。凭借 KGM 的模块化理念,我们可以快速提供量身定制的解决方案。"Knorr说。因此,模块化设计的应用范围远远超出了汽车行业。
“基于伺服凸轮平台的车规级柔性线束装配系统大大提高了客户的装配效率。以前需要花费大量的时间和资源,而现在可以实现快速、高精度、大批量地生产线束。"
本文作者可以追加内容哦 !