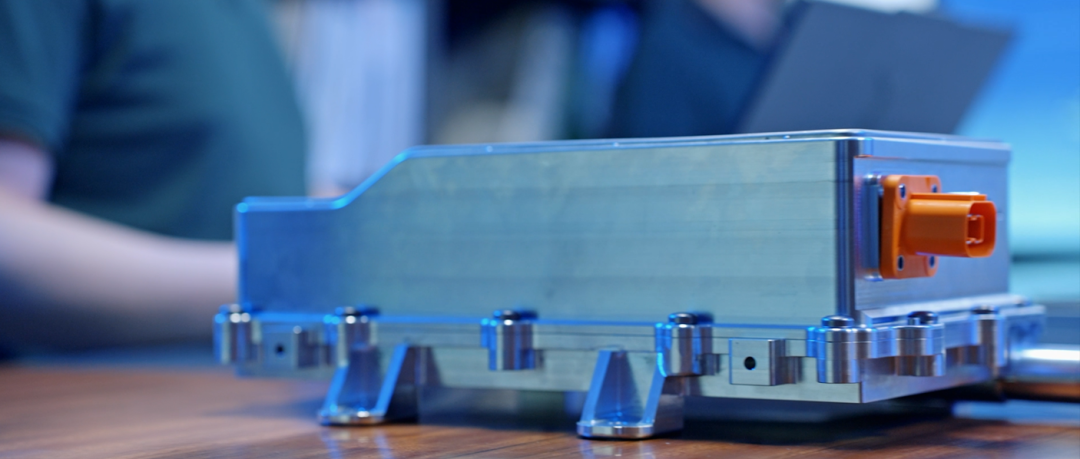
想象一辆电车的“至暗时刻”。年关将至,车票和机票均已售空,你只好开车回北方老家过年。虽然你已经做到“万无一失”——每隔一两百里规划好充电站;全身裹紧厚衣服,减少取暖能耗;老老实实在慢车道匀速爬行。奈何“坐骑”偏偏不争气,1000公里居然充了5次电。望着排队车流,你的崩溃到了顶点:为什么电池总在冬天罢工?
正如“冷水泡不开麦片”,锂离子的运动与环境温度有关,它们特别喜欢在15C—35C之间充放电,超出该范围就会限制充放电的电流。举个极端例子,在零下30C,磷酸铁锂电池的放电功率只有常温的10%。
如何解决?最直接且行之有效的做法就是给电池“加热”。
然而,新能源汽车的电池可是个“庞然大物”,想从低温环境中加热到适宜温度,既要考虑电池能够承受的升温速度,又要考虑热管理系统能够稳定输出的加热功率,还要照顾用户等待暖机的耐心,这些均对“加热器”提出了很高的要求。谁能担此重任?
一条新旧技术的更替曲线正逐步显现。随着新能源汽车开发的深入推进,加热技术也在不断演进——从早期的PTC加热器、电加热器,到近年来兴起的热泵系统,再到如今技术日益成熟并具备更高加热效率的厚膜加热技术。随着厚膜加热技术的广泛应用,未来市场格局会被改写吗?
为何新能源车企都在比拼“热管理”?
去年12月,坐标黑龙江漠河。一场由某头部汽车资讯APP主导的“冬测”拉开序幕。大跌眼镜的是,仅三款车型的纯电续航达成率超过50%。多家车企公开质疑其专业性,甚至有著名CEO亲自下场“硬刚”。
众说纷纭之中,至少有一点可以确定:热管理的好坏,直接影响新能源汽车的续航达成率、能耗增加比例,并最终呈现出不同的用户体验。
燃油车时代,发动机热效率达40%左右,汽车可以回收余热,无需专门制热。电动车时代,发动机下线,三电系统上线,电机效率轻松达到80-90%,没有了“废热”,制热也成为了进步车企们必须啃下的“硬骨头”。
因此,各大厂商都在苦练内功。比亚迪通过E平台三代产品迭代,其一体化热管理系统通过热泵、六通阀等部件,能够实现刀片电池、电驱和座舱三者间的热量互通;小鹏P7热管理系统采用一体化储液罐设计和单热敏电阻加热方案,利用一个四通阀实现整车系统级的热循环。
“领头羊”特斯拉的热管理系统更是经历多次革新——从2000年的分散式热管理应用开始探索,至2020年确定Model Y八通阀技术的高集成度方案——踏上一条从分散到集中、从粗放到精细、从机械化到智能化的演进之路。
1.0热管理系统——Tesla Model S/X车型。引入四通阀控制结构,可实现电机回路与电池回路的串并联模式;空调、电相互并联并独立工作;乘客舱制热通过加热器HVCH( PTC )实现。
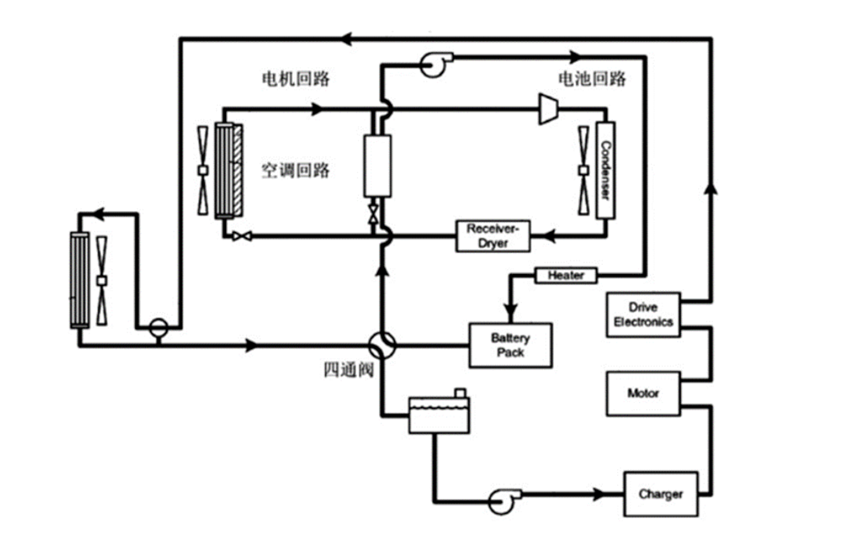
2.0热管理系统——Tesla Model3 /Y车型。Model 3 采用五通阀,并增加新的技术应用;Model Y采用大集成式八通阀,结合热泵、空调系统、加热器、电驱动和电池热管理回路,优化了电机堵转技术、智能热管理算法和标定技术。
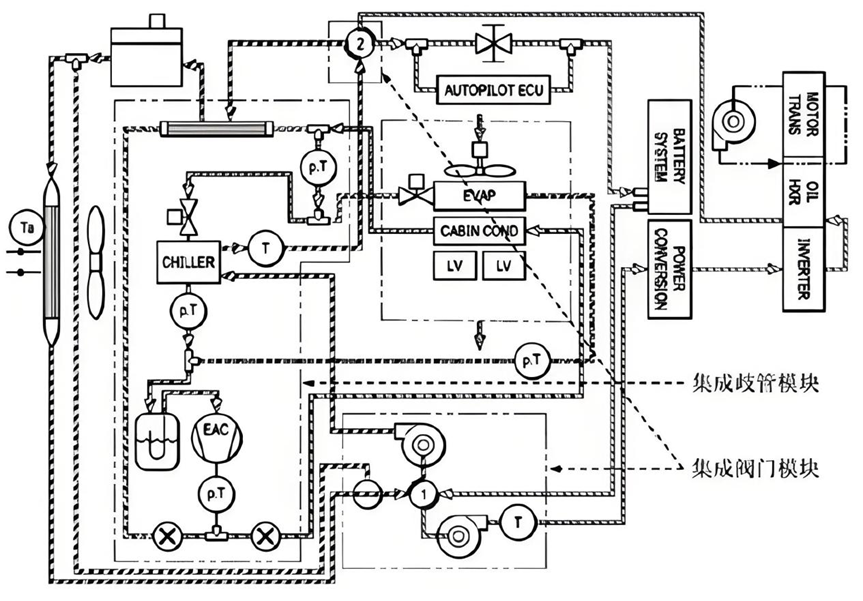
3.0热管理系统——Tesla Model ?目前正在研发中。预计将基于2.0技术架构,进一步优化能量回收系统,系统热管理算法,以及标定技术。
沿着上述整体循环、整体统筹、高度集成的进化方向,未来热管理系统尤其需要提升控制精度、协同能力。其中,新型加热器的重要性凸显。
它应该满足哪些条件?——既能及时、精准地感知系统温度,包括零部件的动态余热;又能稳定、高效地加热,保证所有组件在最佳温度中运行;还能缩短充电时间,延长电池寿命等等。
自身原始性能足够强悍。兼具高效和节能;兼具持久和稳定,在较长时间内保持恒定的功率输出,温度上升并不会导致功率显著下降。
匹配新能源汽车的发展方向。800V高压平台推动整个电动汽车产业链升级换代。这要求包括新型加热器在内的其他高压部件需按照800V 进行设计、开发和验证。同时,适应高度集成的热管理系统。这要求新型加热器不仅要满足闭环功率控制,还能实现多温区梯度设置,便于智能操控。
重中之重,成本一定要更低。新能源车企“卷”字当头,最直观的就是“价格战”。据测算,一台纯电动汽车的热管理系统高达7050元/套,燃油车仅为2800元/套。
开源证券测算,2025年我国汽车热管理系统市场空间有望达1235.6亿元,其中新能源乘用车热管理系统市场空间有望升至880.1亿元,复合年均增长率接近30%。东吴证券测算,国内狭义乘用车热管理系统的市场空间将从2022年的820.80亿元增长至2026年的1320.77亿元,复合增长率为12.63%。基于全球2500万辆计算,2025年整体新能源乘用车热管理市场份额达到1800亿人民币。其中,高压液体加热器预计五年内成长为250亿市场规模,十年内成长为450亿的市场规模。
如果有一种新型加热器同时满足上述所有条件,它一定会成为未来几年的“香饽饽”。
为什么厚膜加热技术是当前最优选?
主流制热模式分化出了两种技术路线——PTC加热器、热泵系统。但二者的关系不是非此即彼,更像是一对“塑料搭子”。为何这么说?
先来看PTC加热器。
PTC,即正温度系数热敏电阻。当环境温度降低,PTC电阻也会降低。此时,在恒定电压下通电,电阻变小会导致电流增大,通电的发热量就会随之变大,就能起到加热的效果。
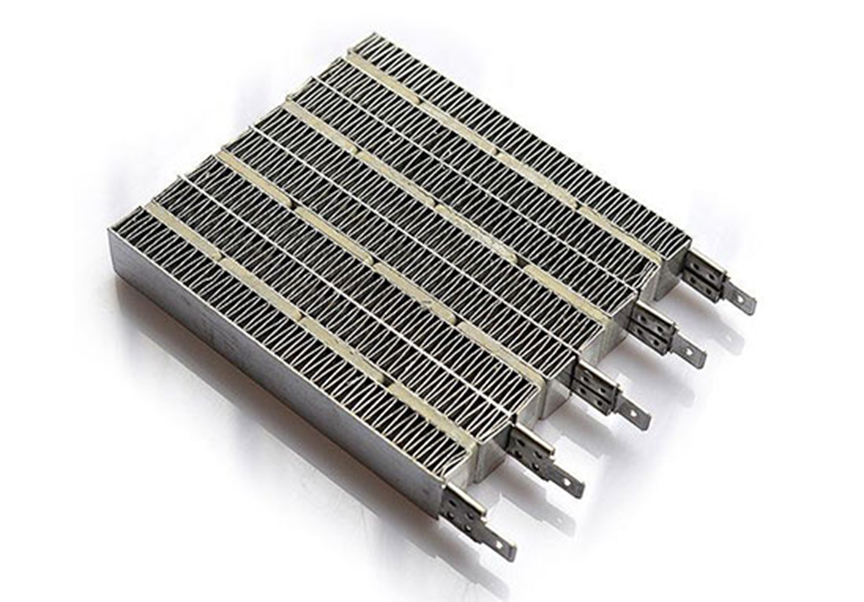
PTC加热存在两种方案,水暖和风暖。前者是通过PTC加热冷却液,再与散热器进行热交换;后者则是冷空气直接与PTC进行换热,最终吹出暖风。
技术已然成熟,问题在于PTC制热能耗很高,严重削减了电动汽车的续航里程。举个例子,一台2kW的PTC加热器,全功率工作一个小时要消耗2度电。如果按照百公里耗15度电计算,2度电约等于13公里的续航里程。在实际情况中,系统还会对PTC的功率进行控制:挡风玻璃除霜,大约需要PTC功率达到2-3kW;加热冷却液,可能需要PTC功率达到6kW左右。
由此,PTC的“塑料搭子”热泵上线了。
热泵,即热量“搬运工”——将低温“物体”,比如车外冷空气的热量吸进来,传递到工质内,再压缩工质使其升温。最终,由高温工质通过冷凝器与车内空气进行换热,实现暖风的功能。
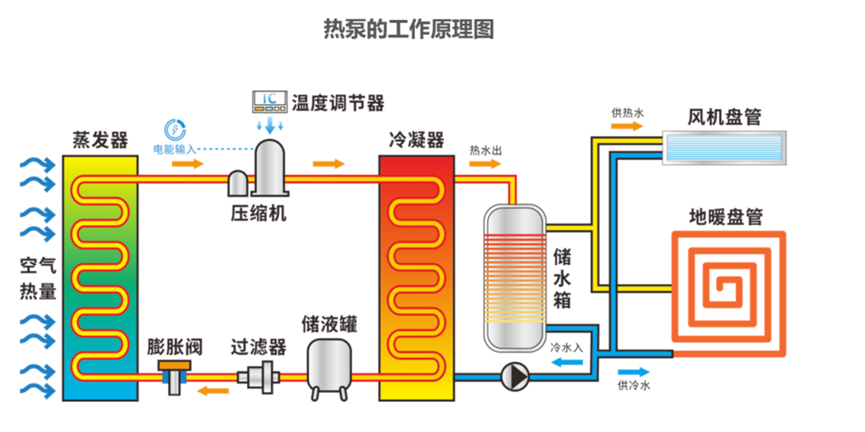
我们可以大致理解为:车内得到的热量=消耗的电能+吸收的低位热能。
消耗的电能仅为驱动压缩机的电机和风机运转的电能。相较之下,空气中能吸收的热能可就大多了。毕竟,从热力学的角度看,只要没到零下273C(绝对零度),外界空气总是有能量的。
我们通常用COP(能效比)衡量空调器性能,COP值越高说明转化效率越高、越节能。理论上,热泵制热COP值达到2-4之间。即,相同能耗下,热泵产生的热量是PTC的2-4倍。
热泵如此优秀,为什么还需要PTC?问题就出在“理论上”。
低温环境中,热泵容易“撂挑子”——零下20C,热泵的COP值会变为1,近乎于不工作的状态;零下10C—0C,热泵的COP值为1-2,就比PTC强了一点。为此,特斯拉会在零下10C—0C启动辅助PTC,帮助制热;等温度超过0C后,又换成热泵工作。高合HiPhi X采用间接式热泵,低温下同样需要将PTC作为辅助热源,快速取暖。
综上,PTC技术简单,缺点是先天能力有限,不稳定且耗电;热泵天花板高,缺点是成本高,且技术不够成熟,未来技术如CO₂热泵尚在发育中,目前需要其他方案打配合。
远水解不了近渴,既能快速替代PTC,又能与热泵重组“好搭子”的方案呼之欲出——厚膜加热技术。
该技术的原理是给导电材料通电,利用电阻加热效应将电能转化为热能。虽然与PTC均为电热转换,但重点正是“导电材料”的区分。
PTC是以BaTiO3为基的半导体陶瓷,具有电阻率随温度升高而增大的特性,导致发热功率不稳。题外话,在1955年,科学家发现,BaTiO3陶瓷中加入微量的稀土元素后,其室温电阻率才大幅度下降。
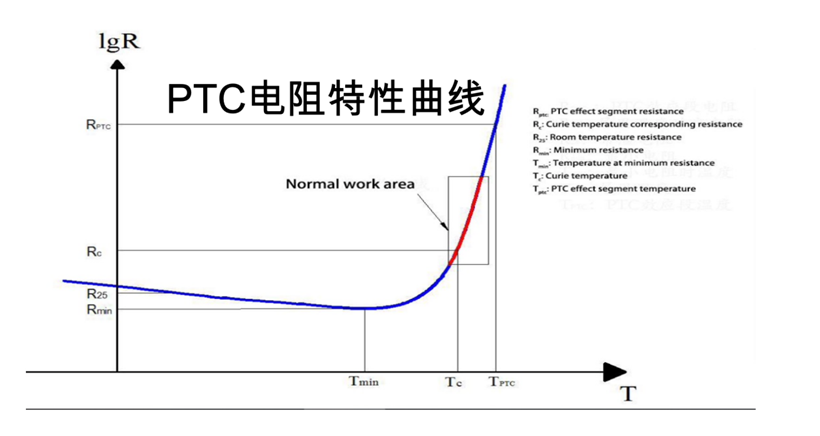
而厚膜加热技术,正是利用稀土厚膜电热材料,在各种基板(不锈钢、氧化铝、氮化铝、玻璃、陶瓷等等)上,通过丝网印刷工艺,进行通电发热,实现从电能到热能的转换。

导电材料和技术原理的不同,直接决定了二者先天性能的优劣。
更协同。厚膜加热器在启动电流、纹波电压及纹波电流方面优于 PTC技术,对整车电气系统影响更小,保证整车性能的稳定性与可靠性,在各种温度条件下均能保持优异的加热效果。
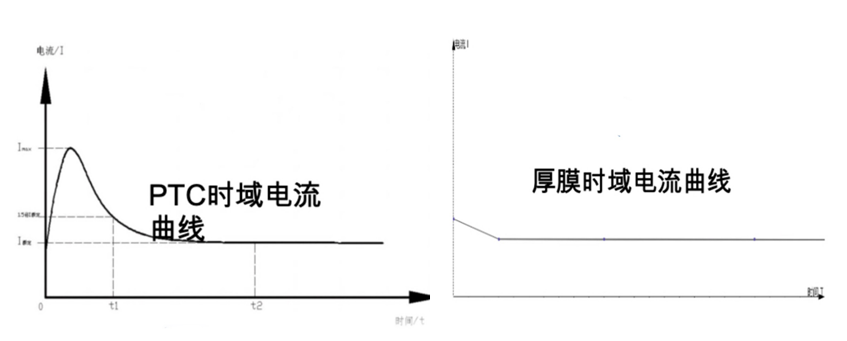
更高效。厚膜加热器的热效率比PTC 技术足足高出7%,既省电,还能显著提高电动汽车的续航里程。
更快速。厚膜加热器的完全启动时间只需30毫秒,而“以快见长”的PTC加热器却需要约 28秒才能达到全功率输出。
更精准。厚膜加热技术采用PWM控制,不仅能做到闭环功率控制,还可以及时、精准地感知系统温度,从而实现更精准的温度控制,满足新一代热管理系统的更高要求。
更稳定。相比于国内PTC 加热器较高的失效率,工艺决定厚膜加热器的制造能被精密控制与严格把关,在质量稳定性、产品一致性。
更长寿。厚膜加热器的功率衰减非常低,在长期使用中可以维持稳定的功率输出,这意味着长寿命与长期高性能。而PTC 加热器功率衰减会随着时间加剧,材料老化会进一步影响其性能。
更划算。厚膜加热技术组装简便、维护成本低等优越特性,使其在成本控制上更具竞争力,展现出广泛的市场应用潜力。
更抗压。在800V高电压平台日益渗透的大背景下,能够稳稳抗住1500V高压的厚膜加热技术,有望替代“限额650V”的PTC技术,成为未来行业的主流选择。此外,厚膜加热器能够完美适应不同规格的电源电压,为多种车型提供选择。
正因如此,随着近两年厚膜加热技术日臻成熟,众多国际知名汽车制造商,如大众、宝马、奔驰、奥迪、沃尔沃开始率先拥抱厚膜加热技术;特斯拉Model 2、本田、丰田、吉利、小米、上汽等品牌正在陆续跟进。
目前,厚膜加热技术小荷才露尖尖角。未来几年内,该技术有望先在中高端车型中取代传统PTC加热器,并逐步应用于中低端车型。谁能在研发上抢占先机,谁就能在新能源汽车热管理领域占据重要市场份额。
掌握核心科技的国产替代标杆
2021年,极氪001搭载着一款新型高压液体加热器(HVCH)闪亮上市。这套神奇的“暖宝宝”采用了厚膜加热元件(TFE),标志着厚膜加热技术在新能源汽车领域落地成熟。
与领先的PCT加热器一样,上述新型厚膜加热器也是由国际厂商制造。同样地,其它HVCH技术,如稀土薄膜,电热管,电阻等等依然由国际厂商主导话语权。然而,在“不出海就出局”的今天,想要满足合规性,完整的本土知识产权愈发重要。
国产替代何时到来?技术突破是关键。
例如,稀土厚膜的升温速率能够从几十到数百C/sec,其秘方在于浆料配制——不同配方对应厚膜不同的功率密度,从而实现温升速率的差异。
又例如,稀土厚膜需要通过类似丝印的技术制备,覆盖在曲/平面的导热基板上。理论来看,曲面厚膜对空间需求更小,承压能力更强,应用范围更广。但在实际印刷制备中,曲面的印刷工艺难度远大于平面。如何保证浆料覆盖的全面性、印刷均匀性与一致性,是制备工艺必须突破的“拦路虎”。
因而无论是浆料配制不均匀导致温度高低不一,抑或是印刷中的杂质影响覆膜效果等等,都可能成为稀土厚膜“爆膜”的元凶。如果厚膜制造厂商只专注于某个生产环节,不具备全套技术开发体系,以及丰富的解决经验,则无法突破根本难题,更何谈量产交付。这正是国际厂商长期占据上风的原因。
近两年,聚焦于愈发成熟的厚膜加热技术,国内初创企业成为了“急先锋”。其中,一支名为苏焱电子的团队崭露头角。
苏焱电子成立于2022年11月,是一家专注于新能源汽车热管理系统开发的企业。公司虽然年轻,但其高管团队均来自全球知名Tier1,具备国际化视野。核心成员已在汽车行业拥有近二十年的创业与从业经历,具备丰富的量产、品控和交付经验。
正是凭借与生俱来的技术基因,苏焱的厚膜加热技术已经解决了三项关键挑战:
其一,高功率密度与轻量化。其中一款产品功率为5KW~9.5KW,重量控制在2Kg,体积不到3L。整套液体加热器具备高功率密度,既能提供足够的热量,又能满足轻量化需求。
其二,高效节能。苏焱电子目前开发的三款产品热效率均大于 95%,高于PTC 技术7%,能够有效提升能源利用效率。
其三,低温性能保障。在相同测试条件下,苏焱产品到达17C仅需25秒,而PTC产品要足足耗费50s。其高效的加热系统确保电池在低温下保持最佳性能。
更为关键的是,苏焱电子拥有完整的本土知识产权,有望实现厚膜加热技术的国产替代。近日,苏焱电子宣布完成千万级人民币天使轮融资,本轮融资由轩元资本领投。目前,公司已建成数十万套的产能,获得多家乘用车和商用车企业的采购订单定点函,并计划在本年度内启动批量生产。
手握热管理核心科技,重视眼下商业化落地,同时紧跟未来市场动态,是苏焱电子成为行业标杆的不二法门。
“短期内,以厚膜加热器为核心,进一步提升产品的市场占有率;在中长期战略中,布局热泵系统,逐步转型为新能源汽车热管理解决方案的全方位提供商。”正如CEO童百灵所言,“苏焱电子将在新能源汽车热管理系统领域占据一席之地,为全球电动汽车市场提供更高效的解决方案。”可以预见,在新能源领域,又一个国产替代的故事正在被书写。
本文作者可以追加内容哦 !