$铁流股份(SH603926)$ $机器人指数ETF(SZ159526)$ #电驱动##超级电机##电机轴##理想汽车##小米汽车##氢能#氢燃料汽车#人形机器人#
目前,新能源汽车对加速性和续航里程的需求和焦虑,对驱动电机的性能和效率提出较高的要求。比如,电驱电机除了满足包络体积小、功率密度大、质量轻;同时还要满足其工作效率高、高效区广等特性。
但新能源汽车驱动电机因为受整车布置空间影响,主机厂一般选用集成化方案。通常在壳体方面,主流方向是将电机壳体、电机控制器壳体、减速箱壳体等三个子系统壳体设计为一体共用;在传动系和电机转轴等关键受力轴齿件,主机厂设计的传动系齿轮一般采用细高齿结构,辅助必要地修形及强化工艺提升强度;轴系方面,则采用挖空轴或者直接空心锻造电机轴或输入轴。
驱动电机作为新能源汽车三大主要零件之一,被誉为“电动汽车的心脏”。在新能源汽车中,驱动电机代替发动机,在电机控制器的控制下,将电能转化为机械能驱动汽车行驶,是纯电动汽车的唯一驱动装置。驱动电机轴是电机系统里的核心零部件之一,其主要作用为传输动力,其性能好坏直接影响到新能源汽车动力系统的性能,工作时需要承受很大的负载和扭矩,因此两端连接部分需要进行热处理,以保证材料的强度和刚性;同时驱动电机轴的加工尺寸精度要求严格,加工需要涉及车削、铣削、钻孔、滚齿等多种加工形式,涵盖热前、热后多种工况,需要搭配高精度、高耐磨及高稳定的刀具才能满足加工要求。电机轴的空心化应该是未来电机轻量化必然路径,也是电驱性能提升的重要方向。空心轴是未来电机转子技术发展的重要趋势。空心轴对于电机系统,不仅仅是明显的减重作用,也对系统冷却布置结构和方式有积极价值。
一、智能电动车时代电机驱动的重要性
电机驱动系统是电动汽车的核心,它与整车动力性能的好坏密切相关,是电动汽车关键技术之一。电机驱动系统由电动机和驱动控制器两部分组成。电动机是一种将电能转变为机械能的装置,为满足整车动力性能的需求,要求其具有瞬时功率大、过载能力强、加速性能好、使用寿命长、调速范围广、减速时实现再生制动能量回馈、效率高、可靠性高等特点。驱动控制器是将电池的电量转变为适于电动机运行的另一种电能变换控制装置。
通过这种变换和控制使电动机处于最佳工作状态,以满足电动汽车实际行驶工况的需要,驱动控制要求结构简单、控制精度高、动态响应好、系统高可靠、成本低,驱动电机及其控制器的性能好坏直接决定车辆的品质好坏。
电机高速化技术通过提高驱动电机的最高转速,可以降低电机的转矩要求,从而减少电机的体积和质量,提高电机的功率密度。同时,高速电机还会推动基于轮毂电机的车辆原地转向、滑板底盘技术的发展。电驱系统最高工作转速行业平均水平为14000 r/min。行业标杆企业的电机转速最高达到17900 r/min,AVL 公司发布的下一代产品电机转速达到30000 r/min,比功率达到7.5 kW/kg。一汽红旗电动车的电机最高工作转速为15000 r/min,略高于行业平均水平。由下表可以看出,当前行业内无论是各大OEM 还是TIER1都呈现电驱系统高速化的趋势,而永磁同步电机作为电驱系统核心部件,易实现电驱系统轻量化、集成化。因此,汽车电驱动在永磁同步电机高速化方面实践具有较大的潜在经济价值。
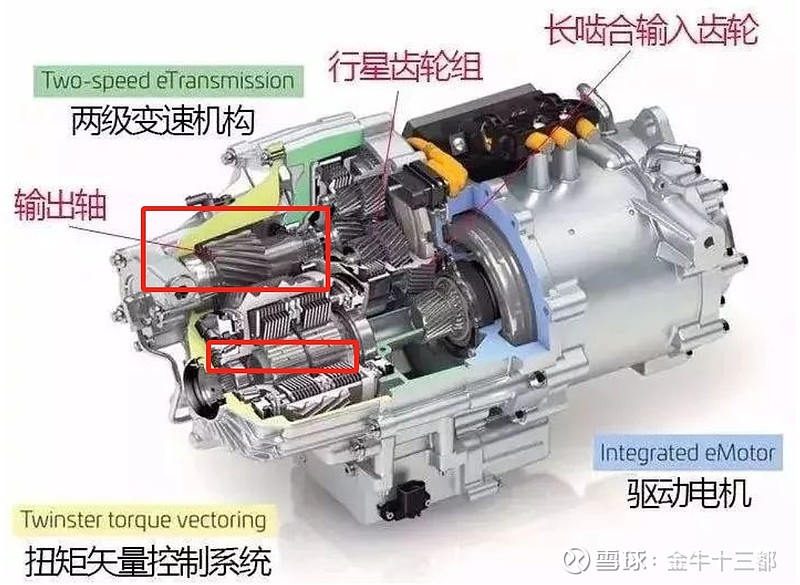
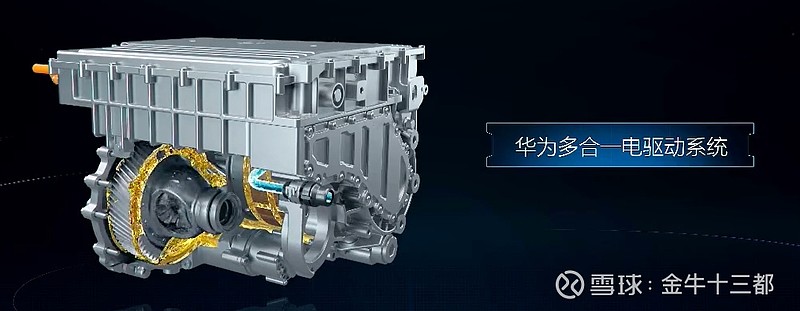
华为十合一电驱动系统:DM(驱动电机)、MCU(逆变器)、GB(减速器)、PDU(高压配电盒)、OBC(充电机)、DCDC(直流变换器)、VCU(整车控制器)、TMCU(热管理控制器)、BMS(电池管理系统)、PTC(加热器)。
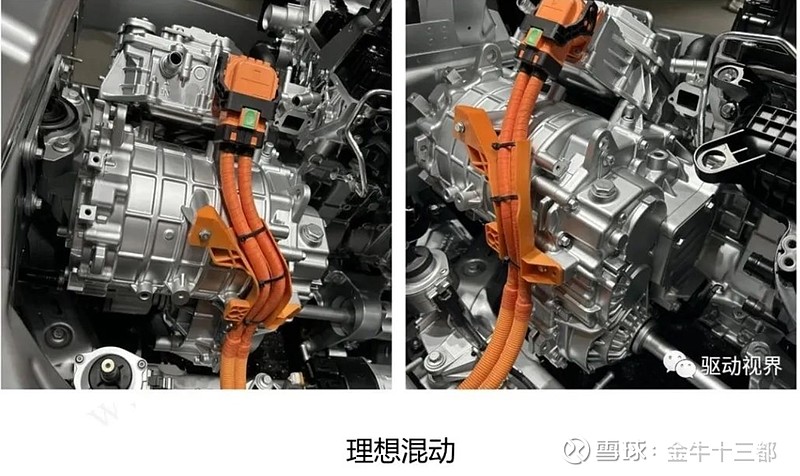
驱动电机系统
驱动电机系统是电动汽车三大核心系统之一,是车辆行驶的主要驱动系统,其特性决定了车辆的主要性能指标,直接影响车辆动力性、经济性和用户驾乘感受。驱动电机系统由整车控制器(VCU)、驱动电机、电机控制器(MCU)、机械传动装置和冷却系统等构成,通过高低压线束、冷却管路与整车其他系统连接。
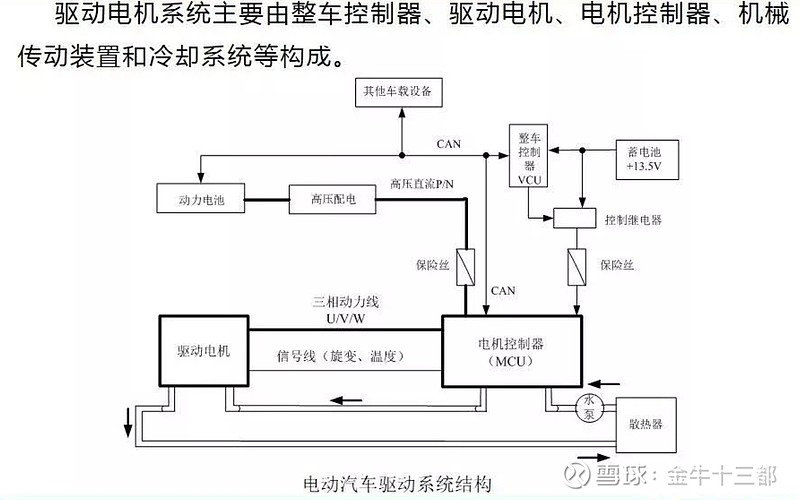
整车控制器(VCU)根据加速踏板、制动踏板、挡位等信号通过CAN网络向电机控制器MCU发送指令,实时调节驱动电机的扭矩输出,以实现整车的怠速、加速、能量回收等功能。
电机控制器能对自身温度、电机的运行温度、转子位置进行实时监测,并把相关信息传递给整车控制器VCU,进而调节水泵和冷却风扇工作,使电机保持在理想温度下工作。
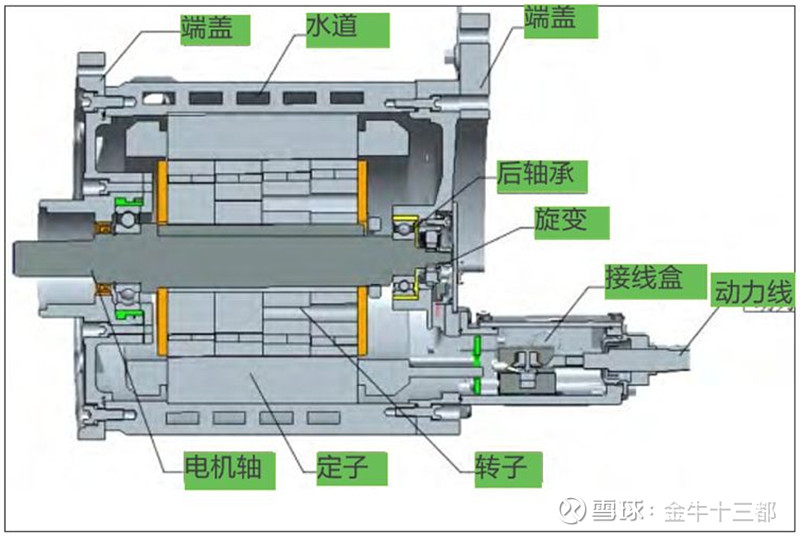
永磁同步电机是一种典型的驱动电机,具有效率高、体积小、可靠性高等优点,是动力系统的执行机构,是电能转化为机械能载体。它依靠内置旋转变压器、温度传感器来提供电机的工作状态信息,并将电机运行状态信息实时发送给MCU。
旋转变压器检测电机转子位置,经过电机控制器内旋变解码器解码后,电机控制器可获知电机当前转子位置,从而控制相应的IGBT功率管导通,按顺序给定子三个线圈通电,驱动电机旋转。
温度传感器的作用是检测电机绕组温度,并提信息供给MCU,再由MCU通过CAN线传给VCU,进而控制水泵工作、水路循环、冷却电子扇工作,调节电机工作温度。
驱动电机上有一个低压接口和三根高压线(V、U、W)接口。电机控制器是通过低压端口获取的电机温度信息和电机转子当前位置信息。
驱动电机控制器
驱动电机控制器MCU结构,它内部采用三相两电平电压源型逆变器,是驱动电机系统的控制核心,称为智能功率模块,它以IGBT(绝缘栅双极型晶体管)为核心,辅以驱动集成电路、主控集成电路。
MCU对所有的输入信号进行处理,并将驱动电机控制系统运行状态信息通过CAN2.0网络发送给整车控制器VCU。驱动电机控制器内含故障诊断电路,当电机出现异常时,达到一定条件后,它将会激活一个错误代码并发送给VCU整车控制器,同时也会储存该故障码和相关数据。
驱动电机控制器主要依靠电流传感器、电压传感器、温度传感器来进行电机运行状态的监测,根据相应参数进行电压、电流的调整控制以及其它控制功能的完成。电流传感器用于检测电机工作实际电流,包括母线电流、三相交流电流。电压传感器用于检测供给电机控制器工作的实际电压,包括动力电池电压、12V蓄电池电压。温度传感器用于检测电机控制系统的工作温度,包括IGBT模块的温度。
驱动电机轴
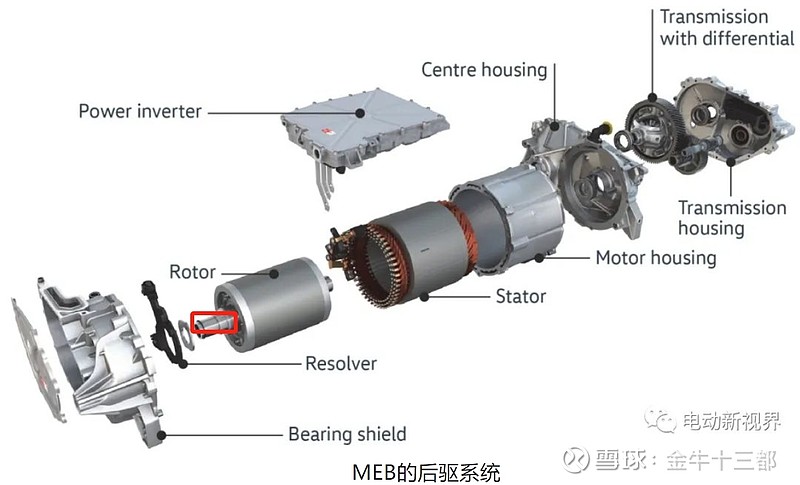
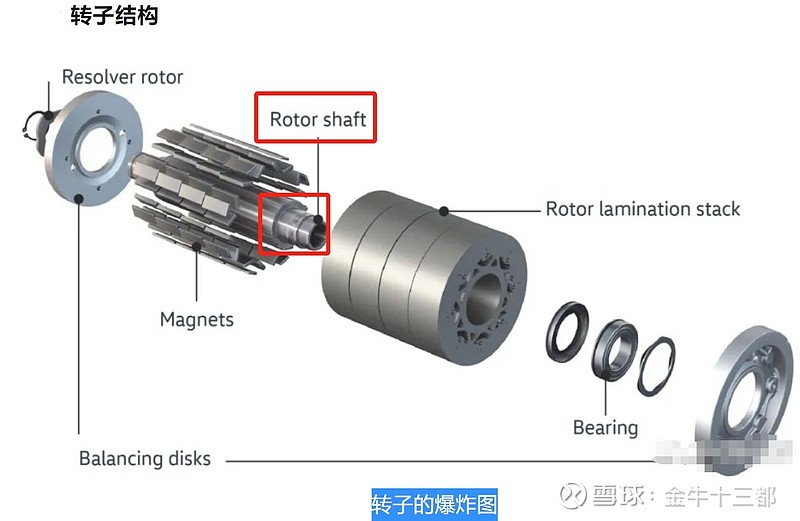
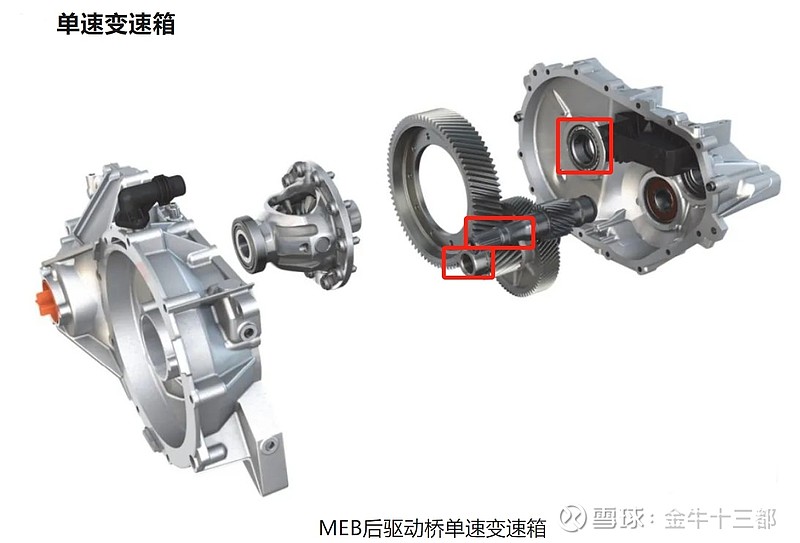
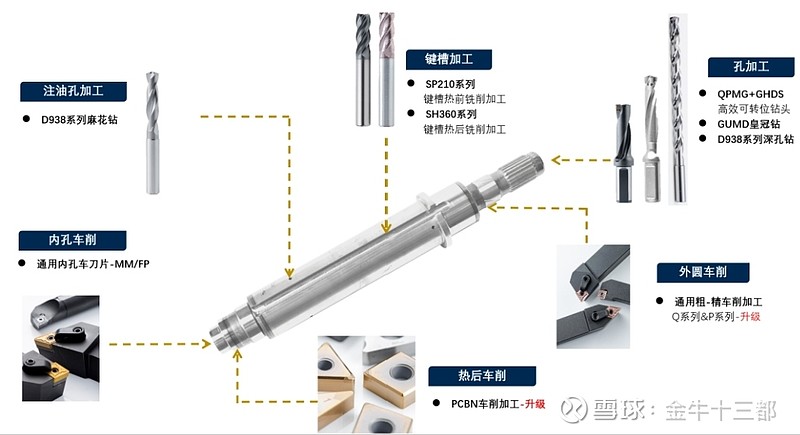
驱动电机作为新能源汽车三大主要零件之一,被誉为“电动汽车的心脏”。在新能源汽车中,驱动电机代替发动机,在电机控制器的控制下,将电能转化为机械能驱动汽车行驶,是纯电动汽车的唯一驱动装置。驱动电机轴是电机系统里的核心零部件之一,其主要作用为传输动力,其性能好坏直接影响到新能源汽车动力系统的性能,工作时需要承受很大的负载和扭矩,因此两端连接部分需要进行热处理,以保证材料的强度和刚性;同时驱动电机轴的加工尺寸精度要求严格,加工需要涉及车削、铣削、钻孔、滚齿等多种加工形式,涵盖热前、热后多种工况,需要搭配高精度、高耐磨及高稳定的刀具才能满足加工要求。
驱动电机主要由定子分总成、转子分总成、壳体、附件等几部分组成,其中转子分总成系统主要是由转子铁心、转轴、轴承等组成。转轴不仅完全承受铁心重量,而且还必须承受在高转速下的不平衡电磁激励作用。
电机轴在使用过程中,其应力往往集中在轴的表面,而芯部仅受较小的弯曲应力,因此,芯部的材料基本属于“多余的死区”。根据材料力学抗弯和抗扭相关公式可知,当空心轴的内外径之比为0.5时,相同外径的空心轴和实心轴的抗弯和抗扭截面系数仅相差6.25%。反推算,在承受相同的扭矩和弯矩条件下,在内外径之比为0.5的空心轴,其外径仅需比实心轴的外径大2%即可满足。换算为质量属性,空心轴重量仅为实心轴的0.78左右,但其减重率却达到20%以上。由此可见,与实心轴相比,空心轴在功用和性能上并没有太大的差距,但是重量却能大幅度降低。因此,电机轴的空心化应该是未来电机轻量化必然路径,也是电驱性能提升的重要方向。空心轴是未来电机转子技术发展的重要趋势。空心轴对于电机系统,不仅仅是明显的减重作用,也对系统冷却布置结构和方式有积极价值。
电机空心轴的制造工艺,一方面涉及传统的热加工领域,如锻造、热处理(正火、渗碳淬火等);另一方面,考虑到装配精度和磁极方向,又涉及冷加工领域,如车削、磨削、插/搓花键等。空心化工艺,可通过实心轴 机加工实现,也可以采用特殊成型设备通过锻造实现空心。一体式成型空心轴,主要是指毛坯的内孔直接成型的轴。目前,应用较广的主要是径向锻造成型和旋转锻造成型。径向锻造和旋转锻造均为特殊成型工艺,主要以进口设备为主。其中,
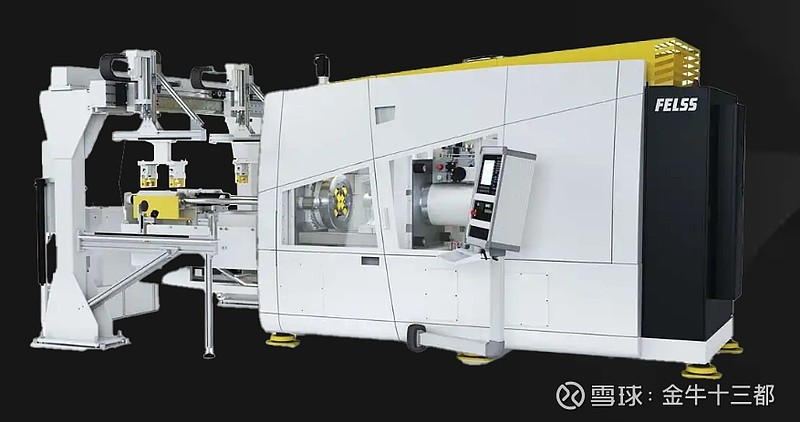
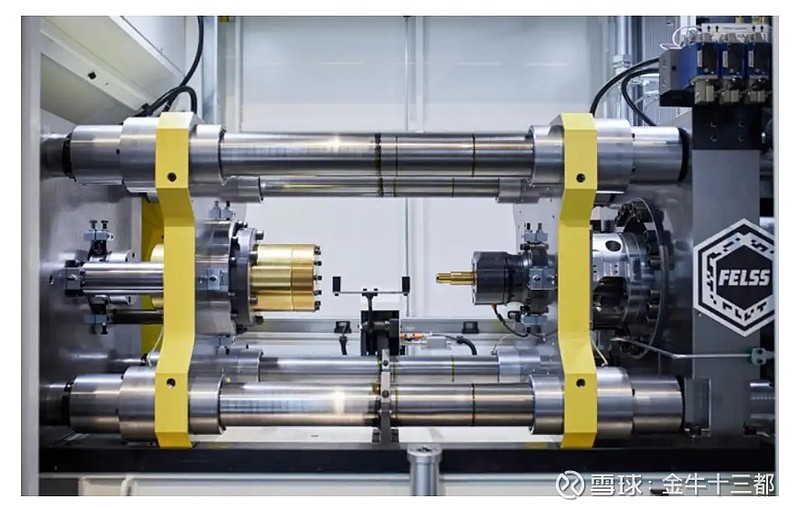
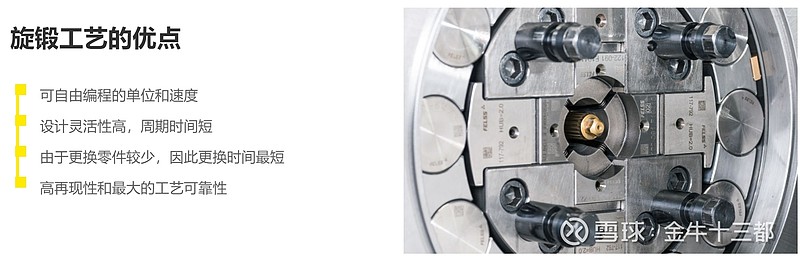
径向锻造成型以德国菲尔斯FELLS公司(网页链接)设备较为典型,
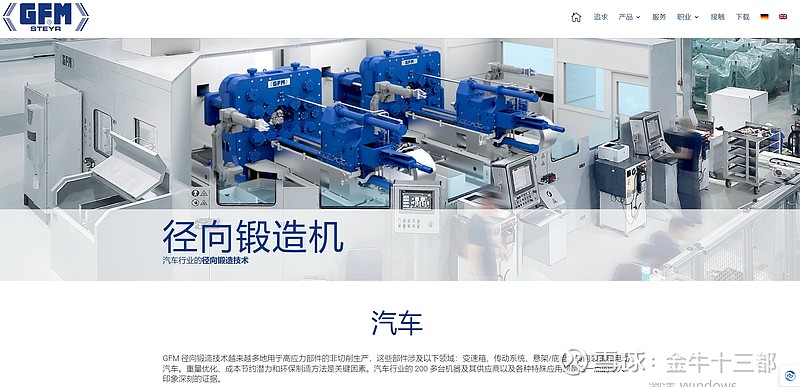
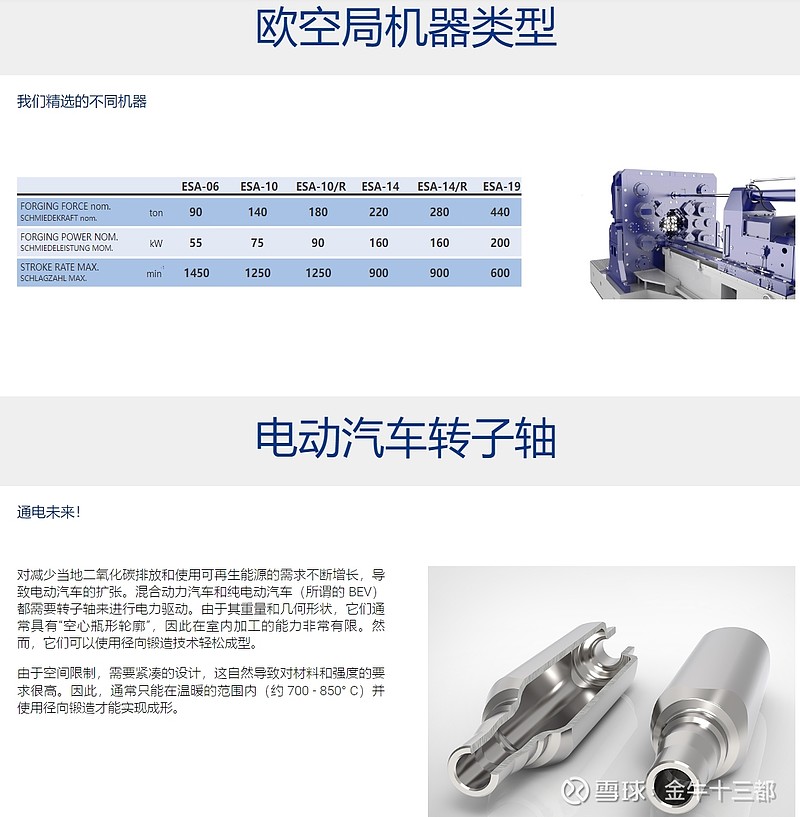
旋转锻造以奥地利GFM公司设备为典型代表。上述设备,不仅可以实现空心轴多台阶变壁厚直接成型,而且可以直接锻出内外花键。径向锻造成型,一般以4个以上对称锤头在每分钟240次以上的高频次锤击下,实现坯料微小变形直接空心管坯成型。电机轴因为结构需要,一般需要二次掉头锻造成型。旋转锻造成型,是在坯料圆周方向均匀布置多个锤头,锤头在对工件进行径向高频锻打的同时绕轴旋转,使坯料横截面尺寸减小,轴向延伸,从而获得工件的一种方法。
二、特斯拉电机电控:集成度高,持续向高能效优化
特斯拉驱动总成:驱动单元集成度高,系统效率提升
Model 3/Y 搭载驱动电机、电机控制器、单挡变速箱三合一驱动系统,集成度高。电机方面,标准续航版后轮搭载永磁同步电机,四驱高性能版后轮搭载永磁同步电机,前轮搭载交流异步电机,采用定子 转自复合油冷系统,Model Y 还采用扁线电机,电机功率密度较大程度改善,成本亦有降低。电控方面,Model 3/Y 搭载 SiC MOSFET,较 Model X/S Si IGBT 方案逆变器功率密度显著提高。同时受益于驱动系统集成化提高、电机电控 等关键零部件升级,Model 3/Y 驱动系统效率达 89%,较 Model S/X 提高了 6pcts。
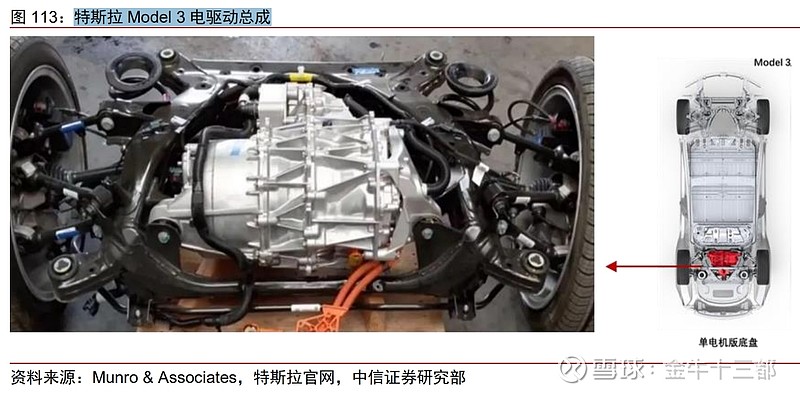
特斯拉驱动电机:向高功率、耗演进,性能和成本持续优化
Model S/X Model 3:由感应电机转向永磁同步电机。2012 年特斯拉 Model S 上市,该车型定位高性能(197kW),彼时大功率车用永磁电机尚未成熟。而大功率感应电机相 对成熟、成本低,且不受稀土资源制约,亦无高温下退磁的担忧。因此 Model S 搭载的是感应电机而没有选择永磁电机。感应电机具备成本低、功率高等优势,但同时也存在体积大、效率低而影响续航等缺点。随着电动化推进,在 2017 年推出的 Model 3 中开始转向使用永磁同步电机。相比感应电机,永磁同步电机体积小更紧凑,效率高而有利于续航且更易控制,在 Model Y 中,特斯拉继续亦采用永磁同步电机方案。
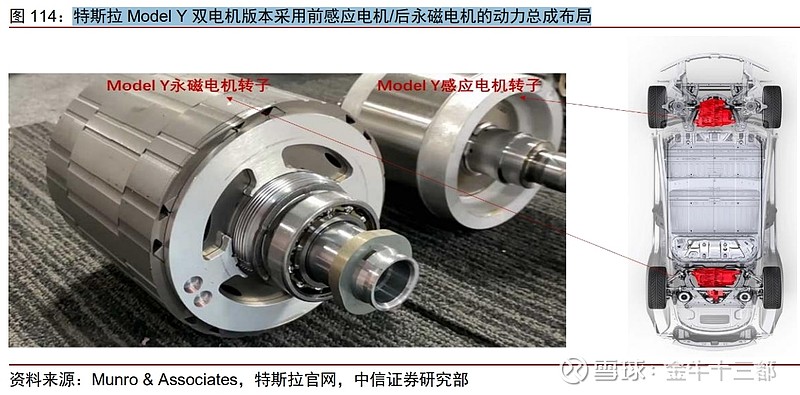
Model S/X→Model 3/Y:双电机版本由前后均为感应电机向前感应后永磁电机转向。2015 年特斯拉推出双电机性能版车型 Model S P85D,在前后轴同时使用交流异步电机。而到 Model 3/Y 的四驱高性能版时,则采用了感应(前) 永磁(后)搭配的方案。主要系感应电机高效区在高速、永磁电机高效区在低速,二者搭配有互补效应。而若采用两档永磁电机或单一大功率电机,成本高、冷却难度增加,实现技术难度较大。
Model3→Model Y:由圆线向扁线切换。目前电机多为圆线电机,绕组一般采用圆形细铜线。扁线电机相比圆线电机的优势在于:1)槽满率 20%提升可使电机体积减小;2)宽截面使其电阻/温升减小 50%/10%左右,输出功率更高,峰值功率密度可达 4.4kW/kg,显著高于目前圆线电机的 3.2-3.3kW/kg;3)在电机损耗中,铜耗占到 65%,而在扁线电机中裸铜槽满率提高,有效绕组电阻降低,进而降低铜损耗。
Model Y 搭载扁线电机,电机体积和功率密度皆有所优化。目前特斯拉在国内共推出 5 款电机,其中扁线永磁同步电机最大功率从 202kW 提升至 220kW,最大扭矩从 404Nm 提升至 440Nm。Model Y 后电机采用扁线方案,扁线漆包线重量约 5.78kg,焊接一致性和饱满性较优,转子体积和重量也皆有降低。预计 Model 3 亦会跟进,示范效应下扁线电机有望加速渗透,比亚迪、蔚来、理想、大众等车企皆开始切换扁线电机。
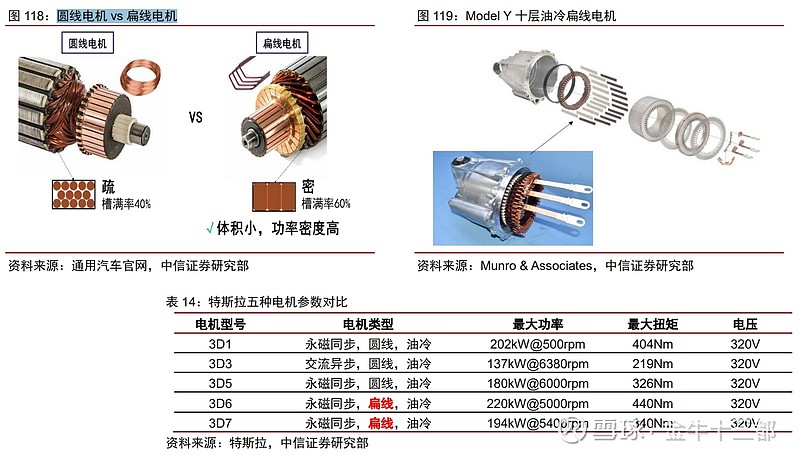
Model S→Model 3:由水冷向油冷切换。早期 Model S 采用水冷系统进行电机热管理,但因是机壳液冷无法对绕组直接冷却,冷却效率较低。后特斯拉电机均以油路冷却方案为主,散热能力和电机功率密度明显提高。
Model 3:采用“定子冷却 转子冷却”复合方案。一方面定子铁芯表面开有 162 个方形油道,与机壳过盈形成油路,两端安装塑料油环(圆周均布 16 油孔)进行绕组两端喷油冷却。另一方面转子轴中空且开有甩油孔,转子主动冷却同时,能通过转子甩油实现定子绕组内圈冷却。Model 3 复合式油冷技术使得电机的功率密度和转矩密度明显提升,相较普通的水冷电机,持续转矩能够提升 40%-50%。
Model Y:整体延用了 Model 3 的油冷方案,在定转子细节上进行优化。新定子铁芯取消了外表面的横纵油道设计,并采用激光焊接,外壳定子进油口和后油环结构发生调整。转子油孔位置和数量更具针对性,甩油效果提高。
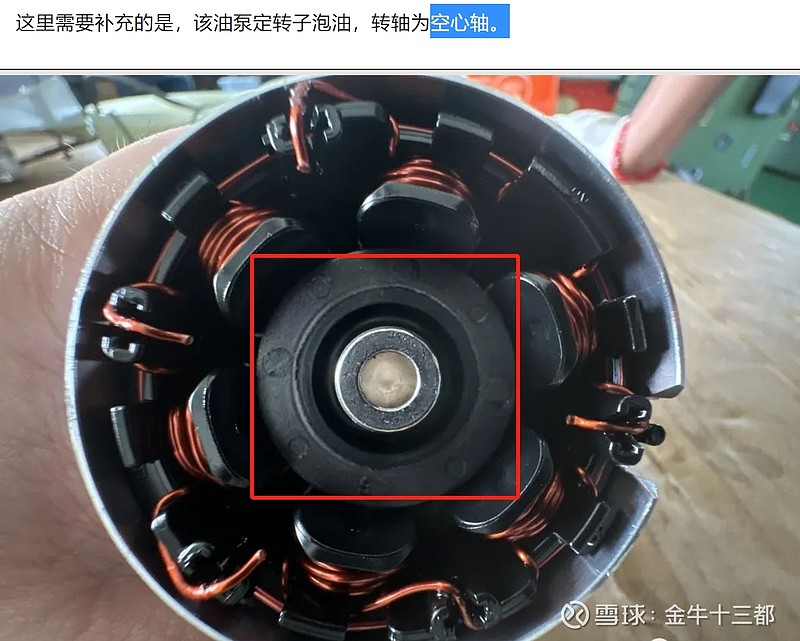
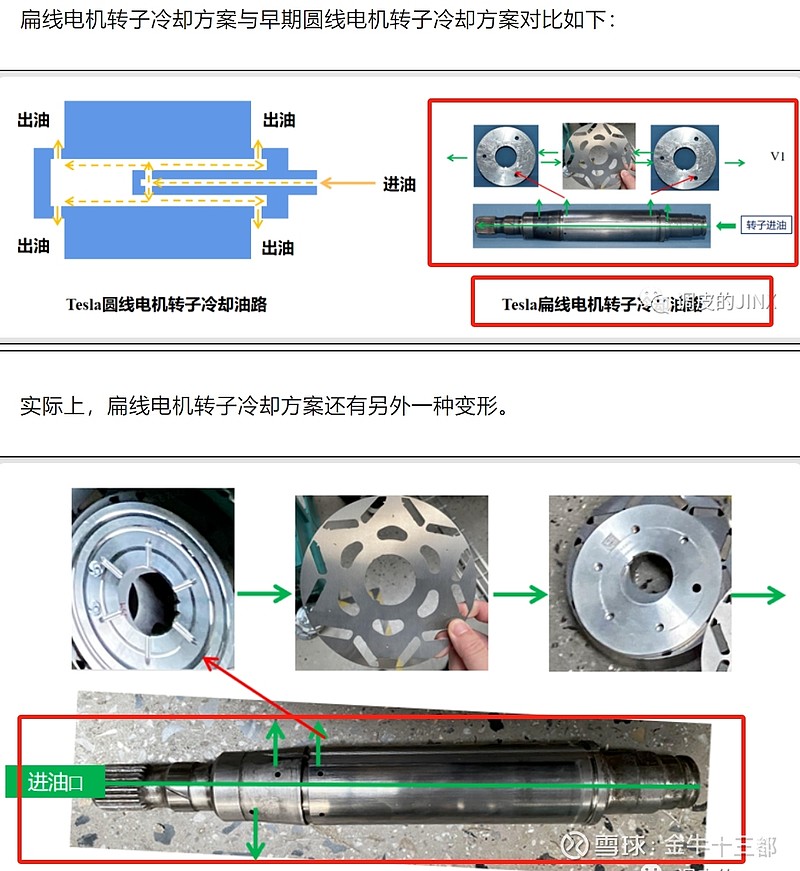
三、小米汽车超级电机,见证性能革命
小米超级电机V6、V6s:21000转
电机是电动汽车最核心的技术,直接决定了汽车的性能。相同扭矩的情况下,转子转动越快,电机的功率越高,车的动力性能就越好。像BBA、保时捷这样的主流豪华品牌,目前已经做到16000转,特斯拉曾经是全球电机天花板,全新Model S Plaid售价接近百万,转速做到了20000转。
所以小米在官宣造车后,首先立项就是做超级电机,而且目标是每项关键技术都做到世界领先。小米汽车从底层技术做起,组建了100人的专家团队,邀请了两家顶级电机公司,并且使用了最先进的AI技术,一次性做出了两款超级电机:V6和V6s,都达到了21000转!目前已量产,将搭载于小米SU7 首批车型上。
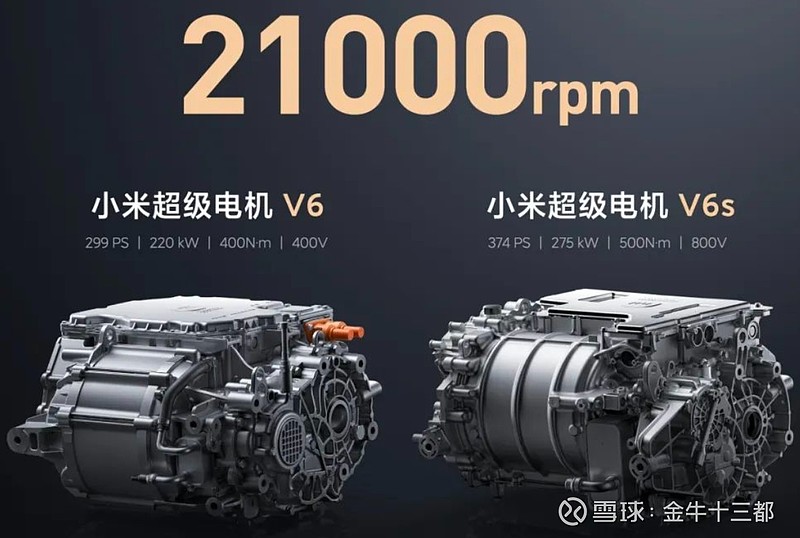
挑战全球电机转速天花板:27200转
还有更不可思议的,是小米首款完全自主研发、自己生产的第三款超级电机:V8s,达到了27200转!实现全球领先电机功率密度10.14kW/kg,成为世界上顶级的电机!
背后的技术难点非常多,第一就是转速带来的巨大离心力,转子容易破碎,那如何提升转子强度呢?特斯拉的办法是在外面裹一层碳纤维,我们则选择直接改进材料,创新超高强度的硅钢,屈服强度达到960MPa!
第二点就是虽然转速提升了,但电机发热非常严重,不能长时间的高转速运行。我们只能重新设计电机散热系统,采用双向立体油冷技术,成功将散热效率提升超过50%,最高温度下降了30%。
最后,我们还重新设计了整个定转子、全系配备自研全球领先的SiC电控模块,转换效率高达99.85%。整个研发过程已申请155项专利,已授权60项专利。
小米超级电机技术预研:35000转 实验已实现
小米汽车团队下决心继续探索科技高峰,已经在预研下一代,创新采用「激光原位固化」工艺来做碳纤维缠绕,这个工艺比特斯拉的湿法缠绕更先进,良率更高。经过大量测试,目前已在实验中成功实现转子35000转最高转速!
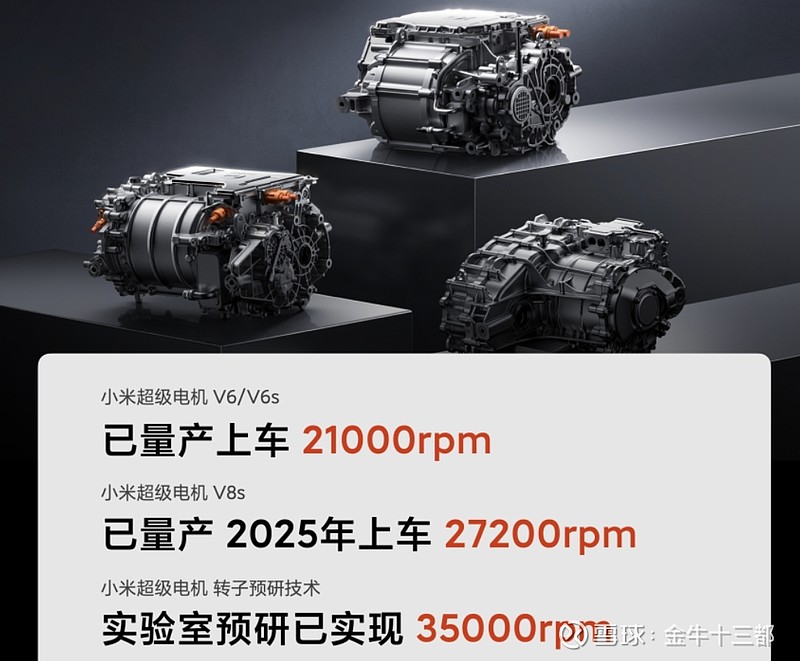
电机技术,我们已实现三代同步研发:成熟一代、研发一代、预研一代。未来,小米也将持续投入电机研发,力争成为行业领导者。
四、铁流股份年产60万套电机轴等新能源汽车核心零件项目
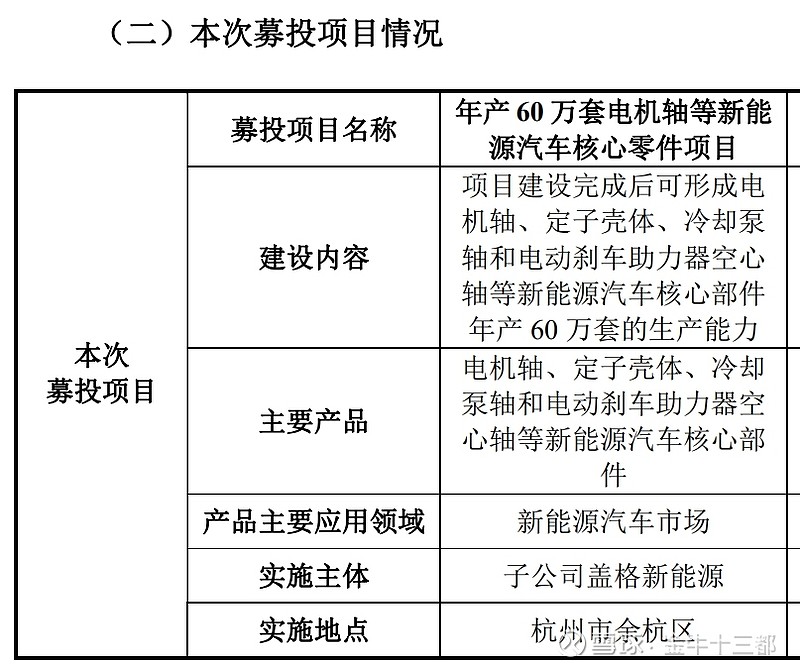
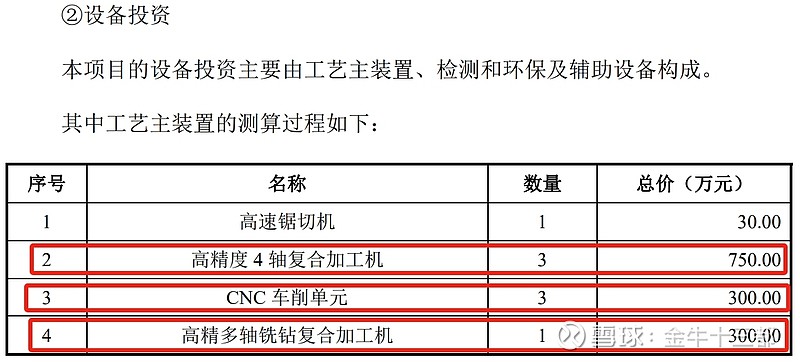
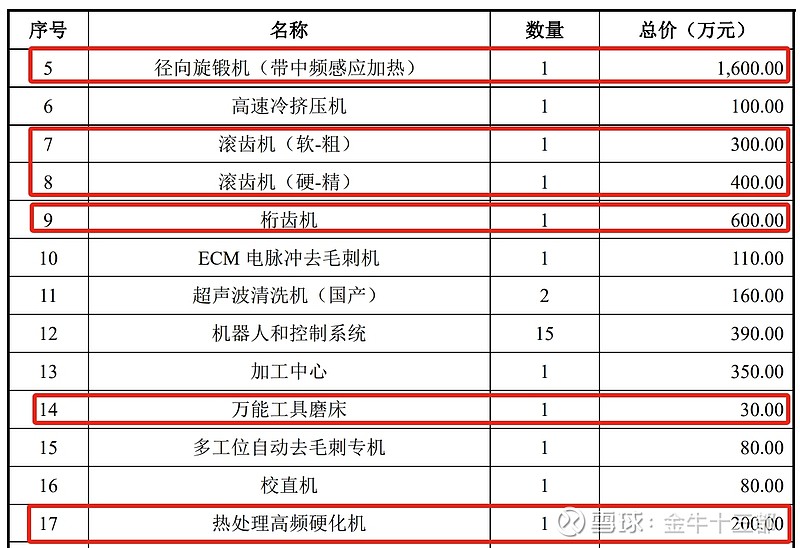
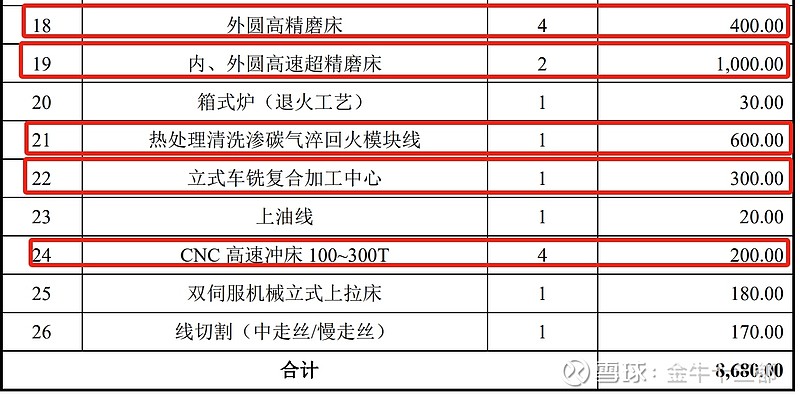
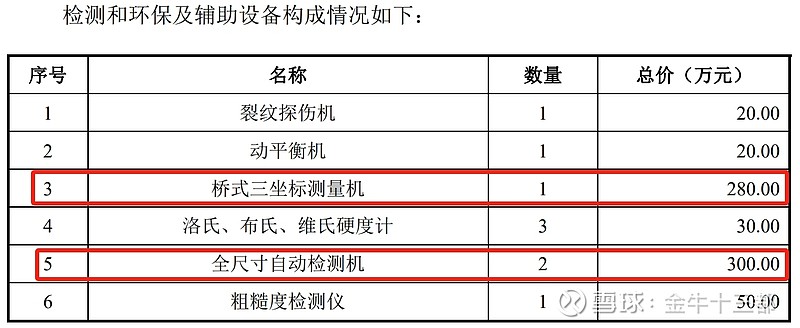
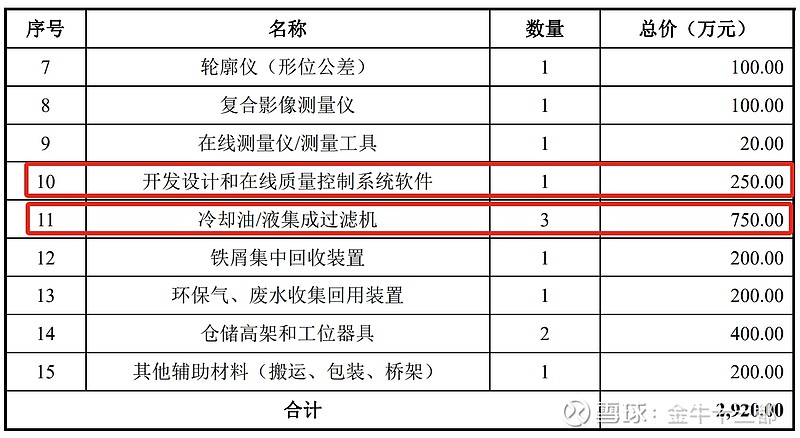
凭借铁流股份德国子公司 Geiger 的自动化生产和精密加工技术,以及其在新能源汽车核心部件领域的产品和技术基础,铁流股份拟建设新能源汽车核心部件制造中心,通过实现新能源汽车核心部件的本土化生产,更好地满足国内新能源汽车生产企业对高精密零部件的加工要求,为国内新能源汽车产业发展提供有力支撑。铁流股份年产60万套电机轴等新能源汽车核心零件项目是铁流股份业务从传统动力汽车零部件向新能源汽车核心部件的扩展,是顺应汽车电动化趋势,保障铁流股份业务持续健康发展的必然要求,项目建设完成后,可形成电机轴、空心轴、定子壳体、冷却泵轴和电动刹车助力器等新能源汽车核心部件年产60万套的生产能力。
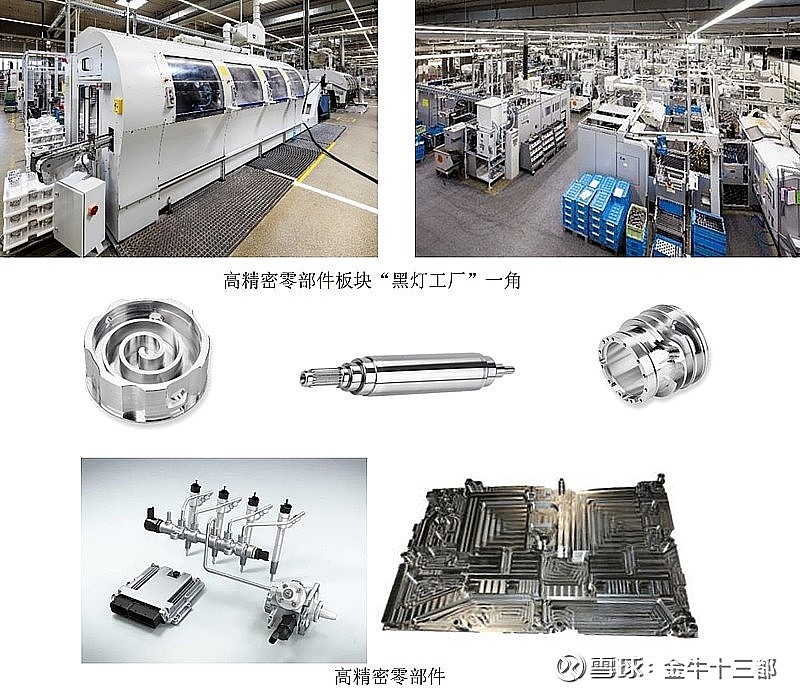
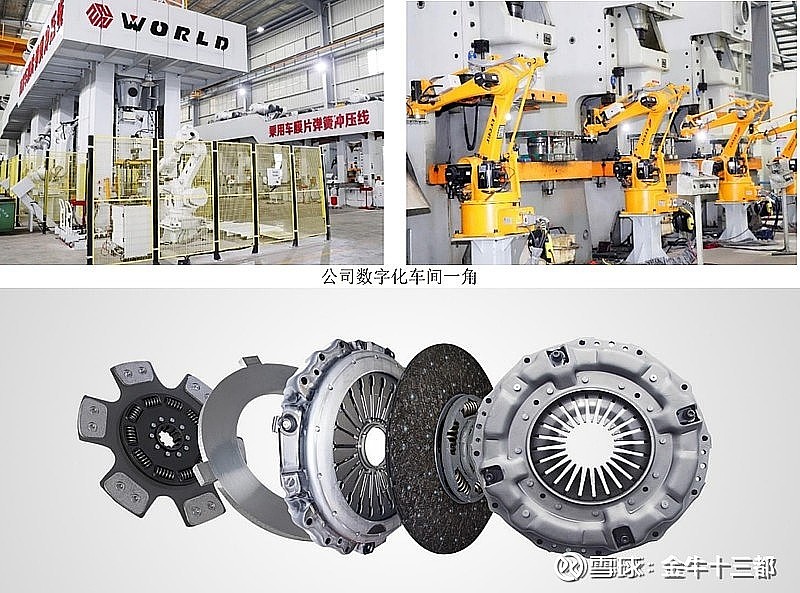
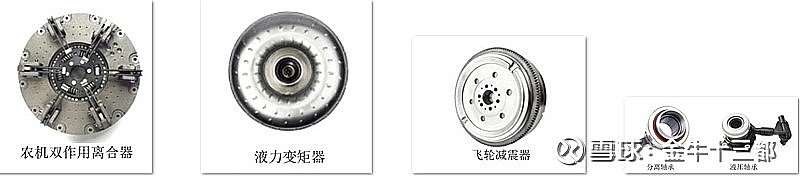
铁流股份子公司 Geiger 拥有超过 20 年的高精密零部件自动化生产线的设计、研发、集成和运营经验,具有领先的仿真模拟、精密检测、高精密金属成型和自动化生产技术,特别是在自动化技术研发设计和精密加工方面具有突出的竞争优势,其配备了 160 多台 CNC 数控加工机床,具有每年开发和制造 2-3 个新自动化生产线的能力,尤其是其自主开发的基于摄像机监视系统的 100%全自动测量控制检测系统能够保证整个产品组的检测效率和灵活性,进一步提高了操作效率并降低了人工成本。子公司盖格新能源一方面吸纳了一批国内专业技术人才,另一方面吸取了 Geiger 公司在精密制造方面积累的经验,为国内多家新能源电驱系统头部企业开发多款电机轴样品,并开始逐步量产。伴随着高端产品从实心轴向空心轴的升级,盖格新能源已投入重量级装备首次打造电机轴空心锻造成型的创新加工方法,在降低材料消耗、提高加工效率、提高零件应用强度和使用寿命上跨入一个新台阶,以引领高端电机轴制造领域。盖格新能源配备了欧洲锻造中心、多轴复合车铣中心和外圆磨、日本双刀架车削中心、高精度滚齿机和四轴加工中心等设备,保证了高端制造加工精度和能力,同时引进了蔡司最新 CMM 测量仪、德国克林贝格齿轮测量机、与德国马尔合作共建的盖格-马尔检测实验室的各类精密测量仪、金相显微镜、自动硬度计等检测设备,能有效保障产品质量。
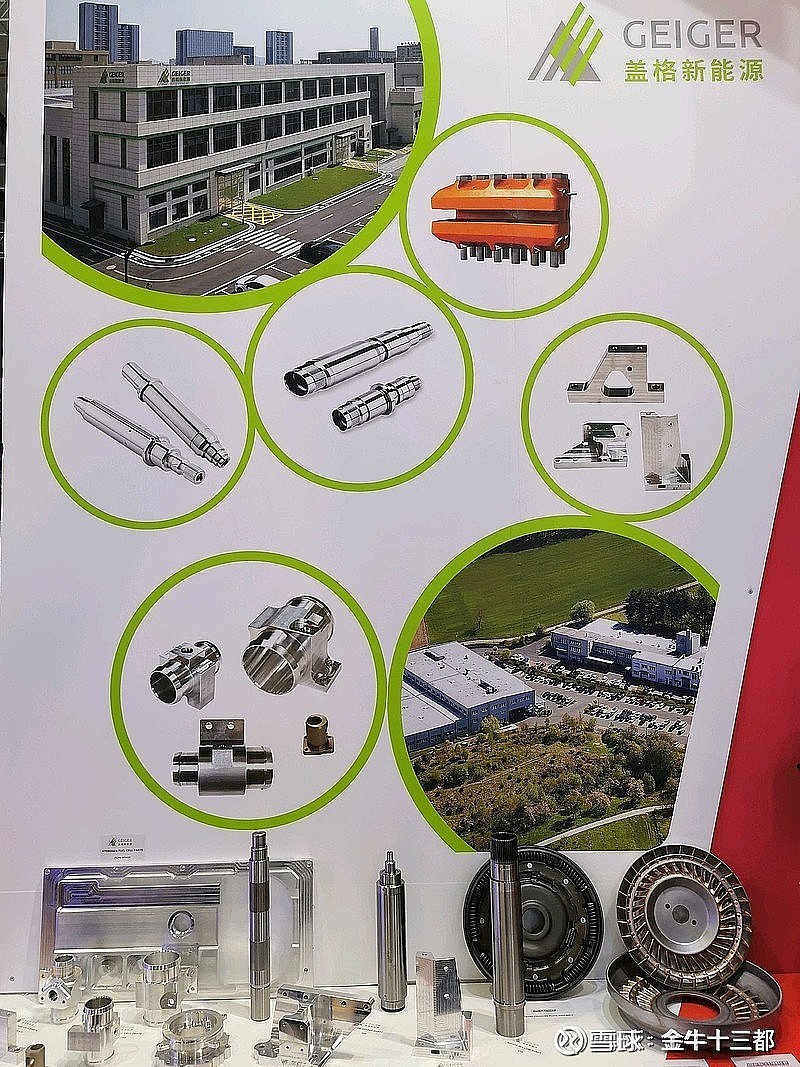
公司配备国内领先的 800 吨压力机和 2,500 吨大型液压机,用于重型车离合器盖的冲压制造,保证产品加工精度和质量,引进日本全套箱式多用炉生产线,采用低碳钢和多种热处理技术,能够保证产品具有优质的耐磨性和韧性,延长产品使用寿命。公司拥有省级离合器企业技术中心、省级企业研究院和行业内首家被 CNAS 评为认可实验室的离合器检测中心,配备了英国 LK 三坐标测量仪、德国 ZEISS 金相显微镜、自行研发的从动盘总成扭转试验机等 70 余台检测设备,具备行业权威的离合器检测能力,有力保证了研发项目的顺利实施。子公司湖北三环引进海外膜片弹簧离合器制造关键设备,后通过自主研发对膜片式离合器进行技术升级,并实现双质量飞轮、飞轮减震器等多项技术突破。湖北三环目前建立的技术中心,被认定为“省级技术中心”,拥有国内离合器领域领先的实验能力,检测试验中心已获得 CNAS 认可证书,是东风、IVECO、玉柴、福特等公司指定的离合器试验基地。
目前杭州总部及湖北三环厂区合计离合器生产能力居全国领先地位,已经成为全国汽车离合器领先的生产和研发基地,在汽车离合器的销售规模及市场占有率方面也处于领先地位,这些都有利于公司在主机配套及售后服务市场保有较高的市场份额,提升市场影响力,从而在原材料采购、产品经销中具有较强的议价能力,有效降低了公司生产成本,提高了产品盈利水平公司拥有较强的新产品开发能力,已开发近两千种型号的汽车离合器产品,可覆盖 90%以上商用车和乘用车车型,高适配性的优势,帮助公司获取了较高的市场份额。公司利用产品数据管理系统形成了对产品系列化、开发流程化管理的自主开发体系,通过内部产品零件标准化工作,提高设计人员的开发能力和产品设计可靠性,已形成了七大系列高新技术产品。其中,耐烧型汽车离合器总成、多适应性可变刚度离合器、JD1000 系列离合器盖总成技术指标达到国际先进水平,具有传动平稳、摩擦系数稳定、使用寿命长等特点。
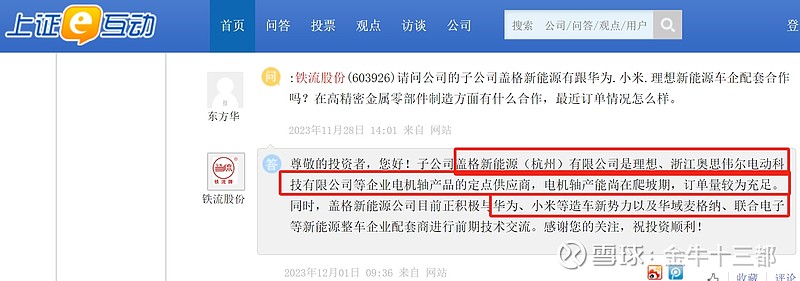
风险提示:本文所提到的观点仅代表个人的意见,所涉及标的不作推荐,据此买卖,风险自负。
本文作者可以追加内容哦 !