$纳科诺尔(SZ832522)$
干法电极:为什么说干法电极是动力电池的未来
作者808, ab
7月 27, 2022
2020年世界范围内对电池的需求量是185GWh,到2030年将超过2000GWh,因此寻找更高效的生产方法成为了电池领域的迫切需要。
4680电芯制造图片
涂布是电池制造过程中的一个关键步骤,将活性物质涂覆在集流体上制作成电极。电化学反应在活性物质中发生,电极因此在充放电过程中可以存储和释放能量。传统涂布属于湿法工艺,将电池材料与水或有机溶剂混合形成流动的浆料,然后把浆料涂覆在金属箔上。
涂布完成之后,电极还要经过干燥和辊压。辊压过程降低电极的孔隙率,因体积减小进而导致能量密度的增加,此外辊压又提升了涂层的粘附与一致性。
湿法涂布干燥过程成本较高,短时间内消耗大量能量,电极完全干燥需要12-24h时间。此外在浆料制备过程中使用的有机溶剂,往往是挥发性的,需要回收并再蒸馏才能再次利用,上述湿法涂布的缺点比较明显,不利于电池市场快速且经济的生产
特斯拉4680电池使用干法电极技术
因此如LG、Samsung、CATL、Ford、GM、Volkswagen以及Tesla公司都在致力于开发干法电极技术,电池产业认识到干法电极的优势因此致力于解决干法电极生产中的相关问题,干法电极将会在下一代电池中投入使用。
干法电极的优势
干法电极技术,将活性物质与特定的粘结剂混合,然后在温度和压力的作用下辊压到金属箔上面,因此不存在传统湿法所需的干燥过程,降低生产成本和能量消耗。
相对于湿法工艺,尽管干法电极经常涉及更复杂的过程,但该技术降低了生产成本和制造时间,同时环境友好。下文将详细分析干法电极的优点。
干法电极生产过程
干法涂布过程需要一些预处理步骤和设备,通过避免使用溶剂,降低总体资本投入和运营费用。由于干法涂布使用的大型设备较少,因此可以使用通常工厂占地面积的十分之一来制造干法电极,这也减少了电池生产过程中的能量需求。并且因干法涂布过程时间更短进而产能更大,这也降低成本减少能耗。确切的讲,干法电极的优点可能使电池成本至少降低10%。
持续性提升
锂离子电池中整个干燥过程所需能耗,占能耗总量大约39%,电极干燥工序大约占据一半消耗。尽管干法电极生产过程仍然需要热辊压,但减少的干燥和溶剂回收环节仍然明显的降低电能消耗和生产成本。另外干法电极生产过程环境友好,因为不需要使用湿法过程中的可挥发溶剂。
干法电极生产示意图
与任何改进工作一样,干法涂布过程也出现很多难题,比如一致性和大规模生产的复杂性。用于干法电极生产的活性混合物,必须在大范围内保持均匀一致。与湿法涂布相似,干法电极仍然需要辊压,而且所需的是热辊压。在特斯拉的生产案例中,混合物意外的使昂贵的压延辊产生凹陷,据马斯克所说,是一个容易解决的工程问题。然而这距离商业化仍然需要大量的实验。
如果干法电极涂层不均匀,可能会在电极中形成所谓的“hot spots”,导致电池电性能衰减、潜在短路甚至灾难性的电池事故。
干法电极自支撑膜
为了保证电池性能,其关键是用最少的粘合剂确保活性材料粘附在箔材上;除此之外,在涂布之前,干混合物必须均匀,混合物中各种材料均匀分布。
一种新的高效技术的开发,离不开对电池制造设备及其改装进行大量投资。特斯拉使用Maxwell开发的干法电极技术,来源于2019年对Maxwell的收购。马斯克(ElonMusk)预估特斯拉将对设备进行五到六次改进,然后才能进行大规模生产。此外,虽然马斯克最初宣布干涂层对行业来说是一个大新闻,然而经过两年的时间,干法电极仍然没有商业化,延迟原因可能是优化工艺过程仍需要大量投资。
3D电极结构能解决干法电极的难题吗
传统电池属于2D电极结构,活性物质涂敷在集流体箔材上。相比之下,新的先进3D电极使用多孔金属结构,在涂层过程中嵌入活性物质。
使用2D箔时涂布层是分层的,电池可能因此缺乏稳定性,这对电极来讲会造成界面分层风险。在Maxwell专利中,曾将集流体表面进行粗糙处理,以防止干粉在集流体表面滑动进而提升粘附性。3D电极可能使该过程更加高效,并因而投入生产应用。
干法电极极片
通过3D电极的应用,活性物质粉末能更容易地从集流体两侧同时嵌入金属框架中,因此均匀性得到提升,这也使得3D电极涂层具有更好的稳定性和粘附性。此外干法电极技术与3D电极相结合的工艺,可以与普通箔材生产相兼容,使用同样生产线。
加速从电动汽车到分布式储能行业的电动化趋势,对于实现以减轻气候变化影响的广泛的低碳目标至关重要。
电池行业需要使用其掌握的所有方法来提高下一代电池的性能、降低成本和扩大规模,而干法电极技术在这方面具有显著的可行性。这不仅关系到更先进电池化学的发展、电极设计的进步如可以促进干法电极改进的3D电极制造方法。
只有当我们关注电池开发的复杂性时,我们才能加快社会未来所依赖的能源转型的步伐。
新能源汽车的快速发展带动了动力电池的高速增长。动力电池生产流程一般可以分为前段、中段和后段三个部分。其中,前段工序包括配料、搅拌、涂布、辊压、分切等,中段工序包括卷绕/叠片、封装、烘干、注液、封口、清洗等,后段主要为化成、分容、PACK等。材料方面主要有正负极材料,隔膜,电解液,集流体,电池包相关的结构胶,缓存,阻燃,隔热,外壳结构材料等材料。 为了更好促进行业人士交流,艾邦搭建有锂电池产业链上下游交流平台,覆盖全产业链,从主机厂,到电池包厂商,正负极材料,隔膜,铝塑膜等企业以及各个工艺过程中的设备厂商,欢迎申请加入。
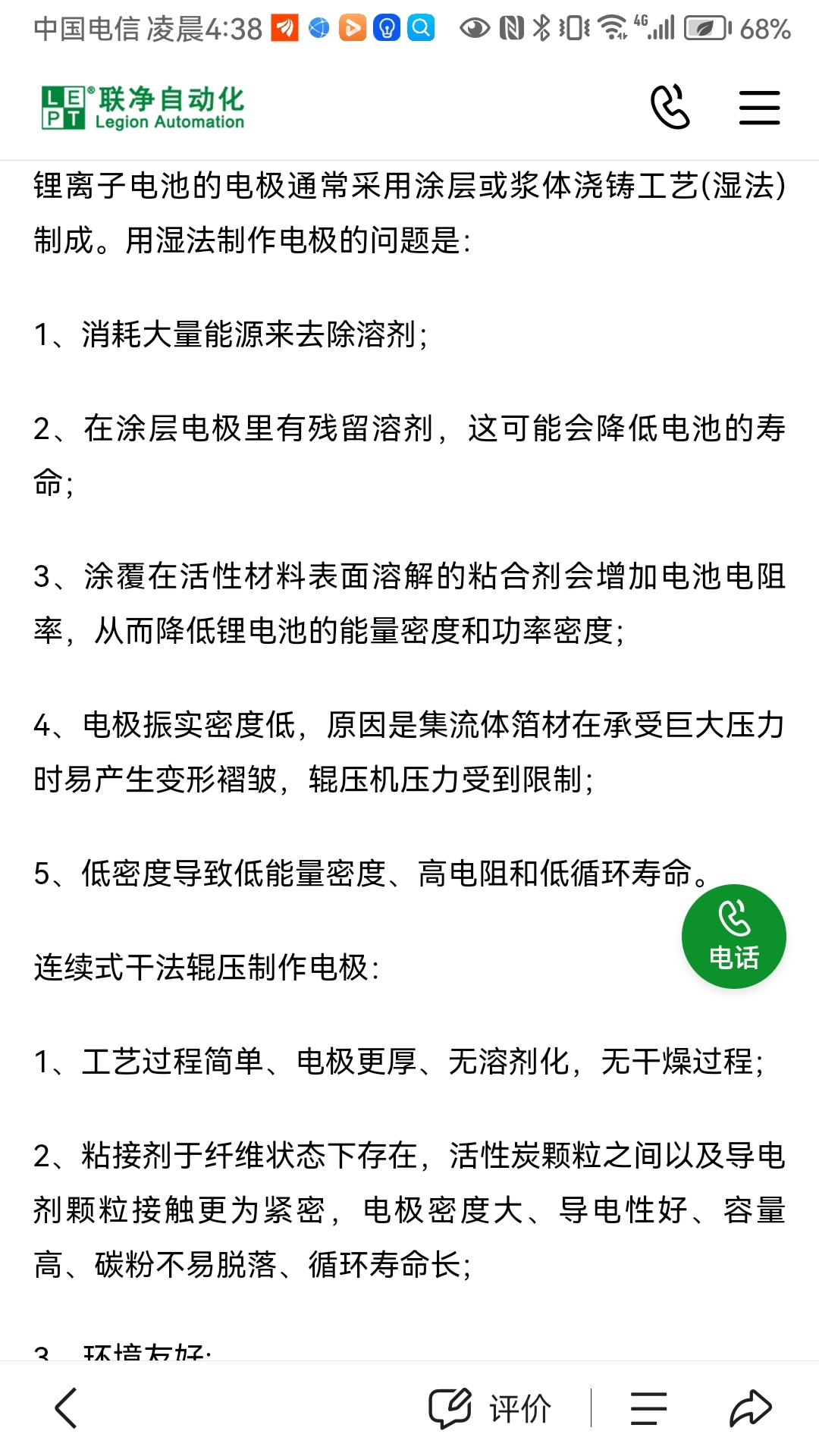
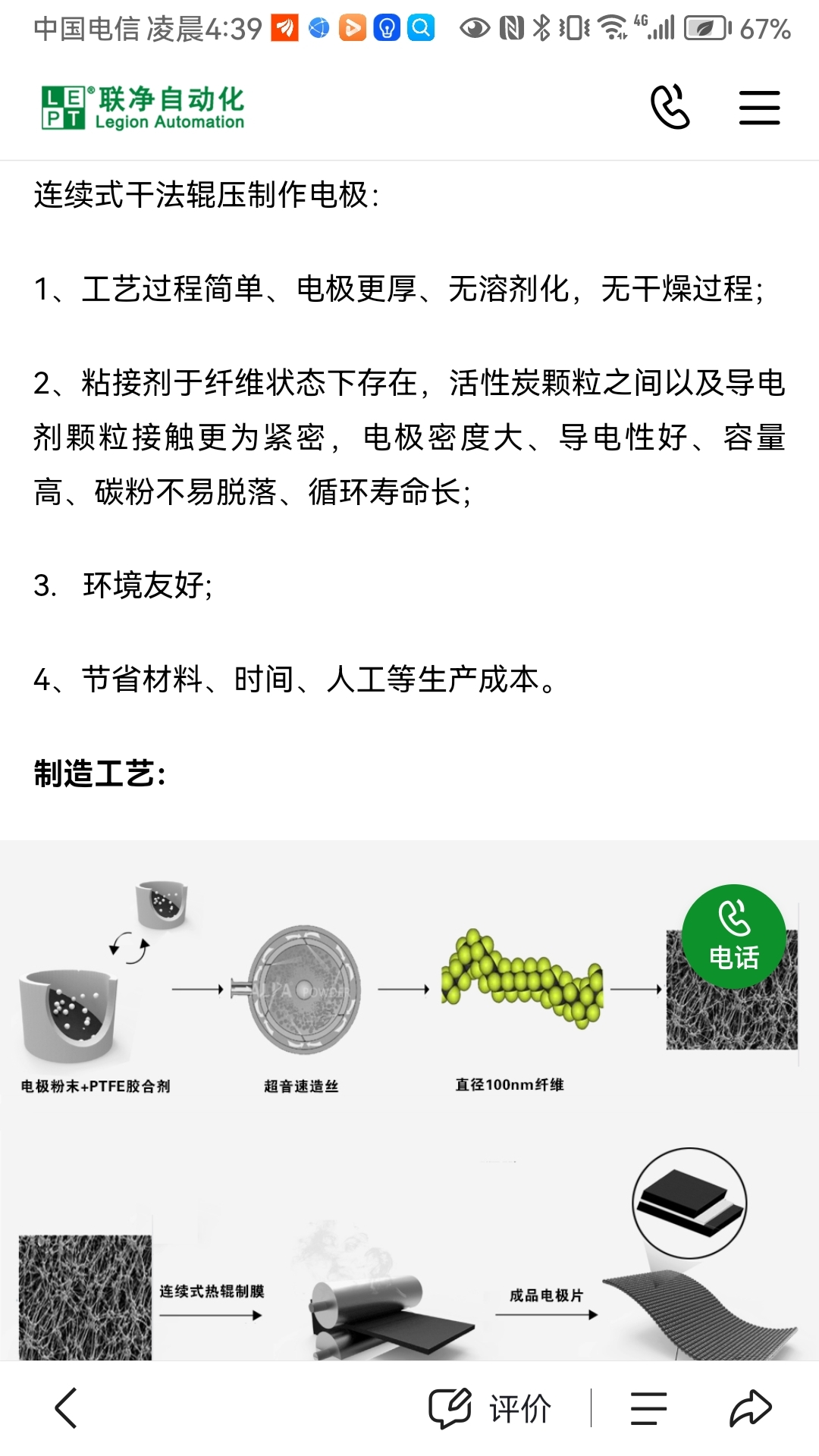
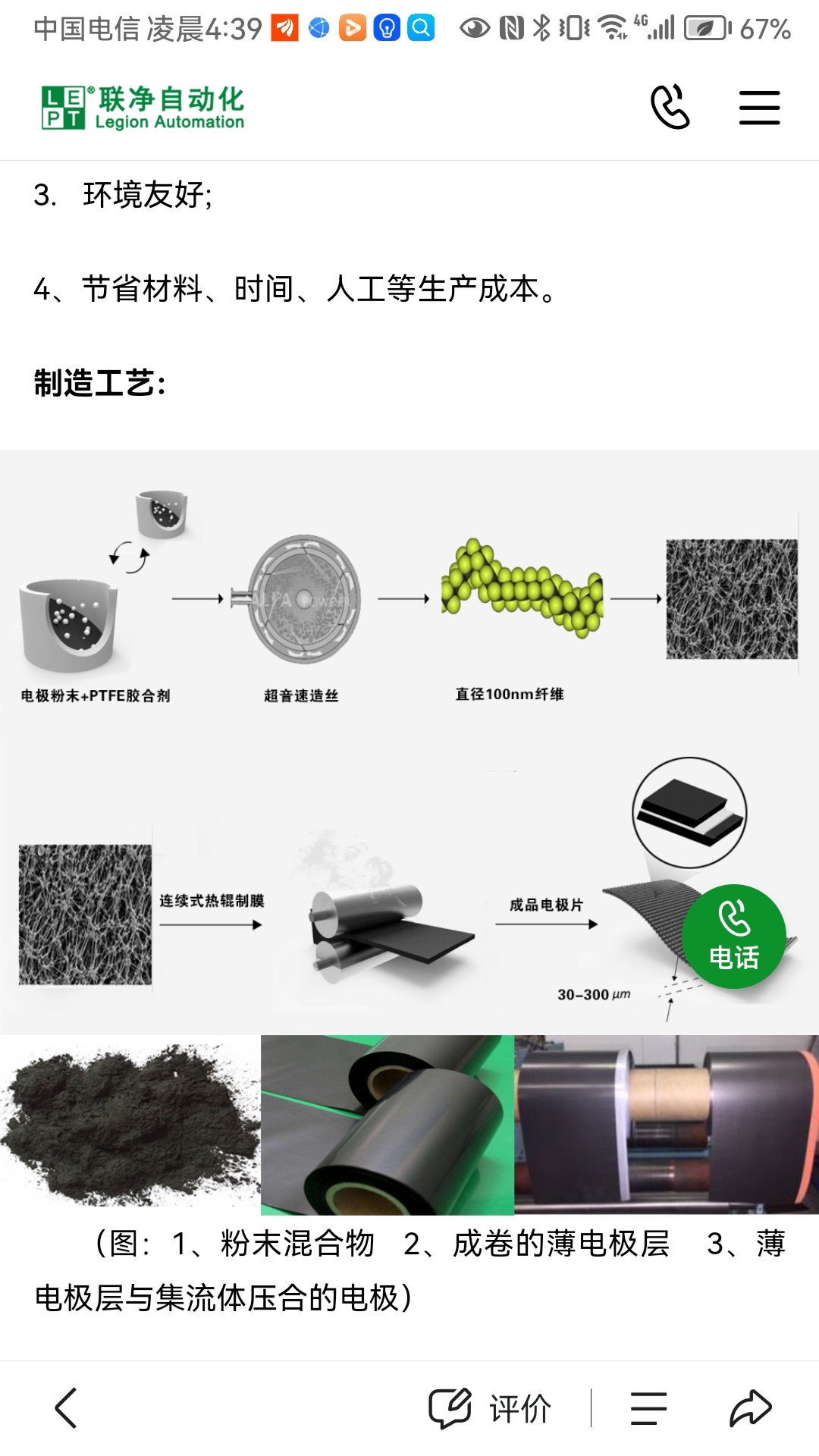
本文作者可以追加内容哦 !