HIsmelt是一种直接熔融还原的炼铁工艺,是典型的一步法熔融还原工艺。该工艺可直接熔炼经预热处理的铁矿粉和其他适合的含铁原料,并喷吹煤粉作为系统的还原剤及热量来源。HIsmelt工艺流程图如下:
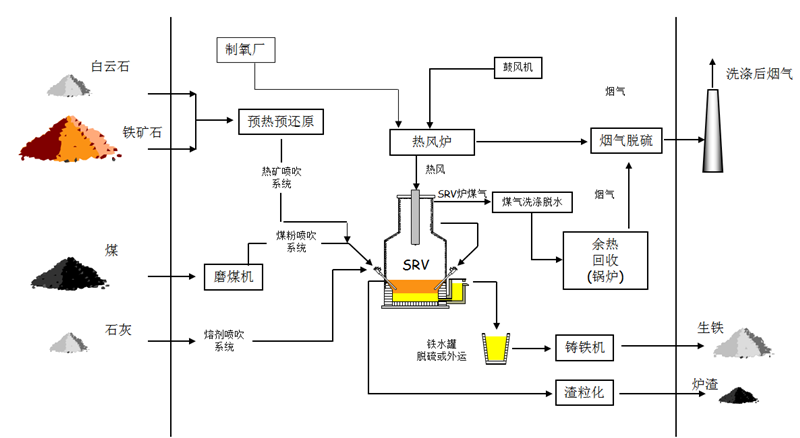
与传统高炉工艺相比,HIsmelt工艺具有如下优势。
(1)较低的投资成本
由于HIsmelt不需要焦炉和烧结厂或球团厂,而且HIsmelt 工艺中的许多设备和设施如热风炉、喷煤系统和电厂等都是高炉炼铁工艺常用的设施,因此工厂建设相对比较简单。此外,由于HIsmelt技术所使用的原料比较灵活,因此无需大型原料配料场,极大降低了HIsmelt工厂的占地面积。
(2)较低的操作成本
由于不需要使用焦炭、烧结矿或球团炉料,可使用更便宜的铁矿粉和非焦煤,并且可直接喷吹工厂废料,因此可取消烧结和焦化厂,炼铁成本较低。
(3)铁水质量好
HIsmelt工艺生产的铁水质量稳定,磷含量很低,基本不含硅,因此可进行少渣炼钢,获得更大的效益。
(4)原料选用灵活度大
HIsmelt工艺直接喷吹铁矿粉(<6mm)(也可以是钢厂细粒度废料和金属粉料、轧钢铁皮粉、经混合的返回料和其它铁料等)。
(5)环保效益显著
因取消焦炉、烧结球团工序环节,大大降低了因烧结、焦化带来的二恶英、呋喃、焦油和酚的污染排放。
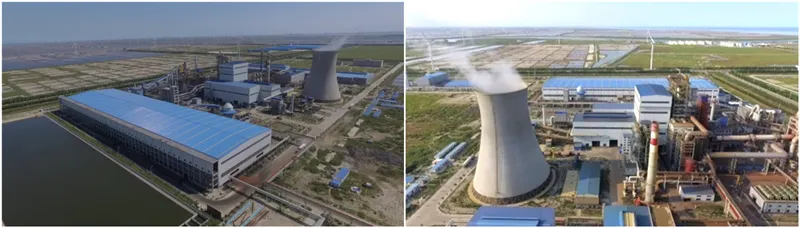
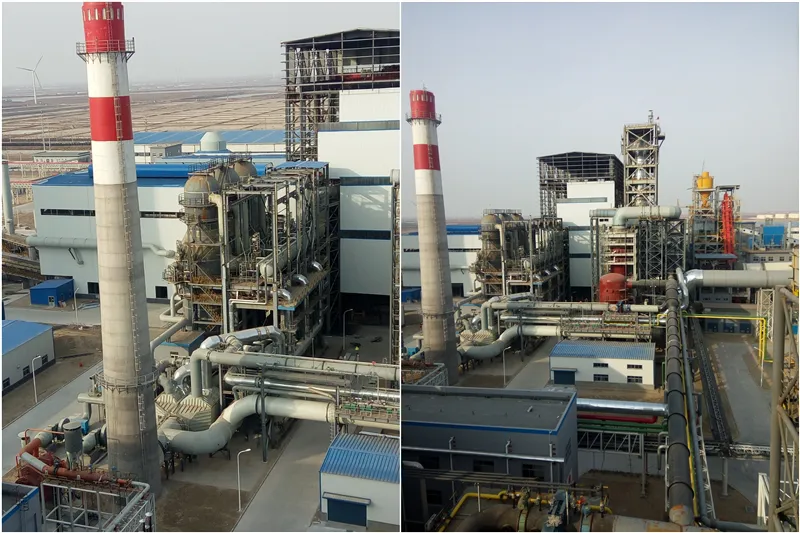
山东墨龙实在是今年ST板块的唯一真龙!
一、超级专利助力中国钢铁绿色发展!
由于过往高炉炼铁一直是主流炼铁技术, 其工艺不仅对环境破坏严重、对优质铁矿石的选择偏向性也导致我国每年要消耗大量优质铁矿石,而我国铁矿石储量低,其大部分还是含磷高、品味低的褐铁矿等,不得不大量进口国外优质铁矿,结果优质铁矿石价格年年增长,下游炼钢企业和制造业苦不堪言,无数老百姓靠双手勤劳挣取的财富,最终却被华尔街大宗投行和已澳大利亚为首的资源国收割!
我国高磷铁矿70亿吨以上,普遍难炼难选,基本都作为“呆矿“未经开发,而以墨龙HIsmelt熔融还原炼铁技术为首的新一代非高炉炼铁法,具有能够消化传统高炉难以冶炼的高磷铁矿的优势,能够彻底摆脱过往对国外优质铁矿石的依赖。
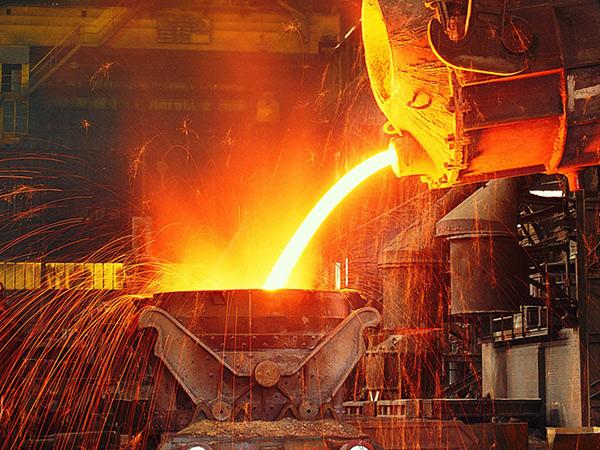
但少有人知,墨龙HIsmelt由于其独特的喷射冶金方式,直接将煤粉与铁矿石喷入熔池中生产液态生铁,具有破坏Tin(碳化钛)、Tic(锑)的反应条件,同样非常适用于冶炼钒钛磁铁矿,可以实现大规模冶炼钒钛磁铁矿甚至全钒钛磁铁矿冶炼的技术目标!
且这一世界技术难题已经在2018年被北科大的科研团队(成员皆是国内冶金系统的顶梁柱人物)所攻关!
而我国钒钛磁铁矿储量巨大,仅攀枝花—西昌一带,就已探明至少150亿吨的钒钛磁铁矿,占据世界钒钛磁铁矿35%以上!
另本本发明还具有有效提升炉渣中TiO2的富集品味,利于后续含钛炉渣中钛资源的高效利用。对于钛以及钒元素这种高附加值又难以开发的资源提取同样具有革命性的意义!
二、HIsmelt就是最大的王牌,专利累计投入算上通胀,至少百亿!
在海外铁矿石居高不下以及我国与主要优质铁矿石资源国澳大利亚交恶的情况下,叠加碳中和环保任务。发展HIsmlte熔融还原工艺已不再是可有可无的选项,而是时不待我,是关乎制造业与基建生死存亡之战,大面积推广墨龙HIsmlte技术刻不容缓!
墨龙HIsmelt工艺发展历程
HIsmelt熔融还原工艺从1980年开始研发,经历了初期的试验炉试验和两个阶段的的试验厂试验后,于2003年在澳大利亚的奎纳纳地区建造了年产80万吨的世界首家商业化工厂(力拓旗下),2008实现设计产能85%。由于受世界金融危机影响,生铁市场低迷,奎纳纳示范厂2008年年底关闭且不再复产。我国山东墨龙公司鬼使神差下于2012年引进了HIsmelt的技术及大部分设备,从2012至2019年,墨龙公司在7年间与国内外大量冶金业的大拿、学者合作,投入巨资(最新数据截止2018年16亿研发资金)通过优化进一步工艺生产流程,前后经过将近10次到付试车,如今已经可以稳定高效生产。
从1980年的基础研发至2021年,历时41年,这41年恰逢中国改革开放,也是中国民营经济从无到有的发展时期。外方在该项技术上倾注了大量的心血和金钱,终于在市场和战略变迁的迫使下,彻底放弃该技术。
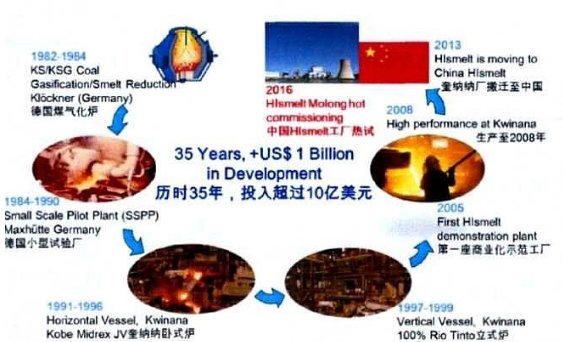
我无意于为这段故事说什么,只是想让读者了解一下一项规模巨大的产业化技术的从研发到商业化的艰辛。
也不得不佩服墨龙的运。
要知道彼时奎纳纳HIsmelt工厂运营期间正置中国钢铁高速发展期,吸引了时任中国国家主席、总理、人大委员长,以及宝钢首钢等35家大型钢铁集团的广泛关注。很多公司都签订了合作协议,一旦成功,将会在中国大范围的推广。由于这是第一个工厂,设备、工艺、技术、人员等等都是全新设计,不可避免的会发生各种各样的状况,始终没有达到预期的运营效果。2008年金融危机蔓延,中国用户的耐心也消耗殆尽,力拓集团和合作方决定西澳关闭工厂。连大企业都搞不定,中国人心里就自然认为该技术已经失败。
历史再次证明,真理往往掌握在少数人手里。
2012年山东寿光一个中型民企企业家通过非直接渠道了解到了该技术,由于该企业(墨龙:正是在下!)恰巧没有高炉,而当时力拓也恰巧才从金融危机的阴影中走出来不得不变卖大量子公司、技术回笼资金,而墨龙上游的炼钢原料由于都从周围高炉企业采购。建设一个年产能不大的生铁生产工厂正好配合其下游炼钢轧钢的车间产能消耗,也就是顺势而为的事情。
100多年前,洋务运动轰轰烈烈,从国外购买技术、中国建厂生产产品,中体而西用之,舍其本求其末,洋务运动最终以失败告终;21世纪的今天,互联网方兴未艾,但中国互联网行业发展的实质是庞大的中国市场,“中体西用”的本质依然没有改变。近俩年炒得火热的芯片事件就是给我们敲响警钟——最核心的技术依然不在国内,中国依然处于世界产业链上较低端的一环。
而HIsmelt知识产权尽归中方所有。知其然,更需知其所以然,在知道如何运营控制的同时,更应该追溯其本源,将基础研究的数据、基本理论、核心工艺参数和设备控制牢牢掌握,让其更加大型化和智能化,形成中方牢不可破的核心技术。
从“0到1”的阶段是痛苦的,如今的HIsmelt技术,承前启后、中西合璧,实现了稳定顺行,这是中国和世界冶金矿产行业的一个巨大进步。随着HIsmelt技术日趋成熟,新项目会不断涌现,单体工厂的产能将进一步提高,年产能200-400万吨的工厂已经有详细图纸。
墨龙HIsmelt熔融还原炼铁技术与其他熔融还原炼铁技术及传统高炉炼铁技术、前景比较目前世界主流炼钢技术分为高炉炼铁和熔融还原,传统高炉面临的技术和碳中和背景下的环境制约众所周知,找到可行替代法是全球炼铁工作者的期盼!
而熔融还原技术一直就是全球炼铁工业的终极目标!
世界上已有熔融还原炼铁工艺约 30 余种,但至今 仅 3 种工艺有较大发展且已经实现工业化,分别为 COREX、HISmelt 和 FINEX 工艺。
COREX工艺流程
国内的COREX是由宝钢集团于2007年花费上百亿引进国外的两套大型COREX3000炼铁生产装置,在上海罗泾建成熔融还原炼铁厂,分别于2007 年 11 月和 2010 年投产。投产后,于各种原因导致COREX 工艺运行不利。为此,搬迁到原燃料(球团矿、原料煤)较有优势的八一钢铁公司,并在COREX3000 的基础上进行优化改造,于 2015 年 7 月 19 日顺利出铁,成功实现了工业化生产,并命名为欧冶炉。
COREX欧冶炉特点:COREX真正的含义是直接用煤作为能源来实现炼铁的终极目标。学名中,CO、RE、EX分别代表Coal-煤,Reductionn-还原、Extreme-终极目标。高炉炼铁所使用的粉矿和资源稀缺的粉煤,必须分别通过烧结厂烧结成烧结矿和炼焦厂将其烧结炼焦成焦炭;而COREX不需要烧结厂和炼焦厂,可以直接使用天然的块矿和块煤,煤块内部的有机物可以在高温下充分裂解,防止焦油、酚、氰等污染物质的产生,单质硫也大部分进入炉渣,大大减轻环境污染。因此,相对于高炉炼铁法来说,COREX熔融还原炼铁技术最明显的特点是炼铁不使用焦炭,无需炼焦工序和烧结工序的辅助,流程和工序相对减少,成本投资和人力使用相对降低,能源消耗和污染排放相对减轻,与完整的传统高炉炼铁过程相比减少13%。
生产状态:欧冶炉 2015 年连续生产 68 天,生产铁水 15.02 万吨,综合厂区周边的煤资源进行了充分的试验,气化炉拱顶喷煤造气的工艺,提升竖炉还原、强化了气化炉造气和熔炼功能,各功能区的效率和稳定性改进。2018 年5 月 26 日开炉,5 天后达到生产以来的最优指标。2018年 8 月,欧冶炉实现月铁水产量 10.5 万吨,燃料比:830kg/t,焦比:200 kg/t,铁水平均含硅 0.8%。
墨龙HIsmelt熔融还原炼铁工艺
HIsmelt工艺具有如下特点
1)投资成本低,Hismelt不需要焦炉和烧结厂或球团厂,因此建设成本降低
2)Hismelt工艺中的许多设备与设施,如热风炉、喷煤系统、发电等都是高炉炼铁工艺的常用设施,因此工厂建设相对简单
3)占地面积相对于高炉缩小80%,土地成本极低
4)操作成本低,直接使用矿粉和煤粉作为原染料炼铁,不用焦炭、球团和烧洁
5)Hismelt技术可直接喷吹传统高炉烧结厂不宜使用的低品味铁矿粉
6)铁水质量好,磷含量稳定,基本不含硅,因此可进行少渣炼钢,降低炼钢成本
7)降低环境影响,通过革命性的工艺创新,取消烧结、焦炉,Hismelt极大的降低了SO2和NOx.基本截止了焦油、二恶英的排放。
生产状态:截止2018年10月数据,当前日最高产量达到1930t,月产量达到51914t,设备不间断作业达157d,各项生产指标均超过原澳大利亚工厂,产品高纯铸造生铁含磷量低,其他五种五害元素(铅、锡、砷、锑和铋)含量非常低,能够满足高端制造业对高纯生铁的需求。
三种工艺对比分析
综合不同工艺技术,就高炉,欧冶炉及墨龙HIsmelt三种不同工艺从原燃料适应性、铁水质量、技术成熟度、投资成本等指标进行比较分析如表。
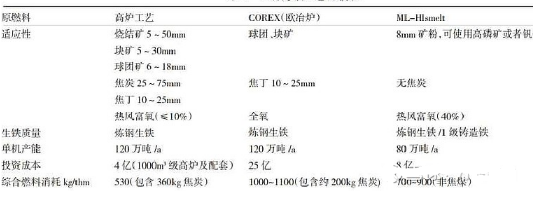
(1)在原燃料适应性上,HIsmelt工艺较好,也是目前唯一不使用焦炭的熔融还原炼铁工艺。同时墨龙HIsmelt技术独特的工艺特性为其在钒钛矿和高磷矿资源利用提供了更多可能,在推动资源利用方面如上文取得新的突破。
(2)技术成熟方面。高炉工艺仍较有优势,但从产业发展趋势来看,未来必被墨龙HIsmelt和欧冶炉取代。
(3)项目投资,高炉投资最低,但如考虑烧结、焦化投资与土地资本,墨龙HIsmelt具有很大优势。
(4)产品质量,墨龙HIsmelt因为独特的冶炼特性,所生产的铁水质量较其他工艺流程而言优势明显,其产品不仅可以做炼钢生铁,也可以做高端铸造原料。
当下公司市值仅20亿,HIsmelt这项技术从立项到商业化光研发资金便超过了80亿,若再考虑到通货膨胀因素(大部分资金是外方在上世纪和本世纪初提供),其研发费用在150亿左右。
山东墨龙HIsmelt技术推广实现突破
去年11月,公司与河北邢钢科技有限公司签署了《技术实施许可合同》,就HIsmelt熔融还原技术实施许可开展合作。本次合作旨在促进HIsmelt熔融还原技术在短流程冶炼领域的应用与推广,将对公司未来经营和发展产生积极影响。
据了解,邢钢集团投资130多亿元实施“转型升级搬迁改造项目”,以响应国家及地方钢铁去产能工作要求,助力区域环境改善。按照相关要求,搬迁项目采用“熔融还原炉+电炉”短流程钢铁冶炼工艺,以1:1的比例实施等量置换,年炼铁产能165万吨,年炼钢产能225万吨。
相较于传统的高炉炼铁,HIsmelt非高炉炼铁工艺不需要焦炭、球团和烧结工序,能够直接使用非焦煤粉与普通矿粉混合,喷吹进SRV炉熔池中冶炼出高纯度铁水,摆脱了传统高炉炼铁对焦煤资源的依赖,同时实现了炼铁全流程的简化,减少了土地与厂房、设备等固定资产的投资,降低了碳排放,被视为可以替代高炉炼铁的最成熟的新技术。同时,HIsmelt+电炉也为电炉短流程炼钢提供了新的方式。目前,公司依托现有HIsmelt熔融还原技术开发的高端铸锻产品已畅销国内外市场,广泛用于核电、风电及高端机床等领域的相关设备制造。
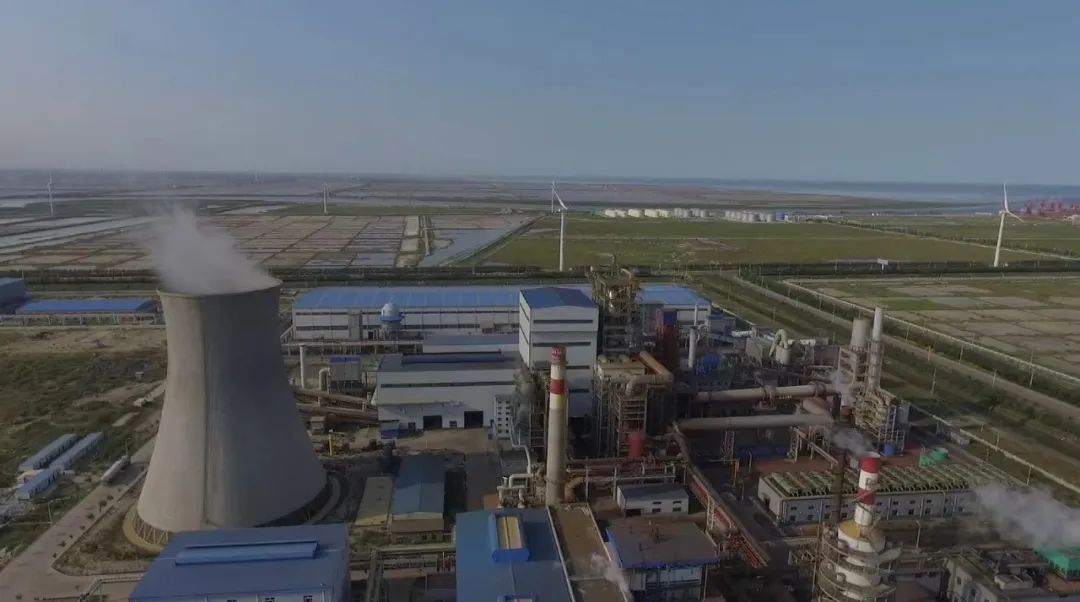
多年来,公司深耕熔融还原技术领域,并致力于HIsmelt技术在钢铁冶炼等领域的应用与推广。作为公司的一项优势技术,HIsmelt技术是山东墨龙积极响应国家制造业转型升级、持续发展循环经济、打造绿色冶金企业的一项熔融还原冶炼工艺。公司已取得全球HIsmelt技术的系列专利与授权,经中国金属协会组织的科技成果鉴定,山东墨龙HIsmelt技术达到国际领先水平。
当前,中国钢铁工业正面临冶炼流程的优化和高质量发展的机遇,废钢铁产业发展较快,将极大地促进与之配套非高炉炼铁产业的发展。直接还原或熔融还原(HIsmelt)+电炉炼钢短流程将为大型钢铁联合企业的转型升级取得技术和生产经验的有力支持(提供新的解决方案)。长流程与短流程的融合将构成中国特色钢铁工业发展的方式,非高炉炼铁的全面发展,对实现我国钢铁工业的绿色发展和转型升级具有重要意义。
学术论文支撑:
王敏:熔融还原炼铁最新技术及工艺路线选择探讨
全 文 如 下

熔融还原炼铁最新技术及工艺路线选择探讨
王敏,任荣霞,董洪旺,张广杰,刘思远
(唐钢国际工程技术股份有限公司炼铁事业部, 河北 唐山 063000)
摘要: 熔融还原炼铁工艺是非高炉炼铁的重要工艺,也是未来炼铁工艺的重要研发方向,目前投入商业化生产的熔融还原炼铁工艺主要有COREX、FINEX、HIsmelt工艺。为了更及时地了解熔融还原炼铁工艺的最新技术动态,有针对性地选择熔融还原炼铁工艺路线,根据近年来对上述3种主要熔融还原炼铁工艺的技术追踪和研究,阐述了中国在引进、消化COREX工艺过程中,在原燃料优化、解决预还原竖炉黏结问题以及工艺控制系统优化取得的技术进步。介绍了韩国浦项公司FINEX工艺在预还原流化床大型化、降低流化床系统高度、能源高效利用等方面的最新技术成果。并对中国引进HIsmelt熔融还原炼铁工艺后,对HIsmelt工艺未来的技术发展方向提出建议和展望。最后,从原燃料条件、炼铁-炼钢工艺路线、产品质量等方面,对如何选择熔融还原炼铁工艺路线提出建议。
关键词: 熔融还原炼铁; 非高炉炼铁; 流化床; COREX; FINEX; HIsmelt
高炉炼铁流程在中国炼铁生产中占据着垄断地位,需要配备烧结、焦化等原燃料工序为高炉提供适宜的原燃料,烧结、焦化、炼铁3大工序占吨钢能耗的85%以上。但是由于高炉长流程中的烧结工序的SO2、NOx、粉尘、二英和焦化工序的水污染物、粉尘排放占钢铁生产排放总量的50%以上,烧结厂、焦化厂已经成为各地区环境治理行动中的众矢之的,长流程炼铁工艺的高能耗、高污染、高排放迫切需要淘汰落后及过剩产能、转型升级、实现绿色低碳生产。留给钢铁产业的选择,除了压缩产能、逐渐提高工艺生产中的废钢比例,降低铁水比例以外,有限的选择方向之一是改变钢铁工艺的原燃料结构,逐渐由传统流程转向钢铁生产短流程方向发展。熔融还原炼铁工艺是非高炉炼铁的重要工艺路线,也是未来炼铁工艺的重要研发方向,是典型的炼铁生产短流程工艺,具有低成本、耗、低碳、低排放等特点,是国家鼓励发展的非高炉炼铁工艺。目前世界上实现工业化生产的熔融还原炼铁工艺主要有3种,分别是COREX工艺、FINEX工艺和HIsmelt工艺,中国宝武钢铁公司对COREX工艺经历了从引进、消化、吸收到创新的过程,FINEX工艺近年来也有国内钢铁企业与韩国浦项公司进行了深入的技术交流和技术引进谈判,HIsmelt工艺国内引进时间相对较短,目前正处于消化、吸收的阶段,国内炼铁工作者对HIsmelt工艺也在进行深入研究。对这3种主要的熔融还原炼铁工艺进行深入和持续的技术跟踪、技术研究,有助于中国非高炉炼铁工艺的技术进步,对企业因地制宜选择适宜的熔融还原炼铁工艺具有重要意义。
1.1COREX工艺
COREX工艺是由奥钢联公司研发的熔融还原炼铁工艺,1989年在南非开始工业化运行,目前南非、印度、韩国拥有建成的COREX装置,中国宝钢引进了两套大型COREX-C3000熔融还原炼铁生产装置,每套设计年产能150万t。2007年11月在上海罗泾建成投产,实现了连续4年顺行生产,对中国非高炉炼铁技术的发展及人才培养,掌握熔融还原炼铁工艺的生产组织和操作、相关工艺设备制造和维护都做出了重大贡献。COREX工艺流程如图1所示。
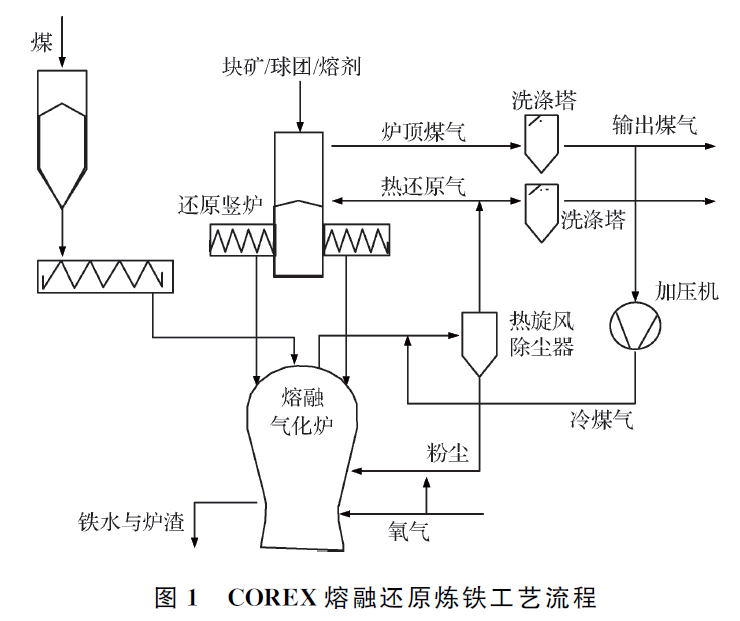
2012年宝钢公司将COREX工艺装置搬迁至新疆八一钢铁公司,经过改进设计后,将之命名为欧冶炉,2015年短暂开炉生产后,经过1年半的优化改造,技术提升,于2017年3月25日点火复产,复产后生产情况稳定顺行,生产成本日益降低。欧冶炉是中国炼铁工作者在COREX-C3000基础上,对COREX工艺的一次有效提升和再创新,结合新疆地区的资源禀赋,发展了具有八钢特色的熔融还原炼铁技术。
(1)欧冶炉优化了还原竖炉煤气管道布置,促使还原煤气流合理分布,有效解决了COREX还原竖炉的黏结问题,提升了竖炉金属化率。
(2)将炉顶煤气湿法除尘改造为干法除尘,增加了TRT的发电量,达到55 kW/t(铁),同时极大节约了水资源,提高了煤气利用率。
(3)优化了炉体冷却结构和冷却水系统设计,合理分布炉体冷却强度,改善炉体寿命,保证炉况顺行。
(4)优化入炉原料结构,用烧结矿替代价格较高的球团矿,烧结矿比例最终达到40%,炉况稳定顺行,欧冶炉能够处理含锌粉尘及城市废弃物,并对欧冶炉原燃料供应系统和出铁出渣系统进行了进一步改造升级。
(5)优化了生产工艺控制系统。建立了欧冶炉物料平衡和热平衡模型,提升了还原煤气温度及成分控制,优化了气化炉炉顶煤气操作控制。
相比于目前世界上存在的COREX工艺(印度4套,南非1套),中国炼铁技术人员在工程设计、生产组织、设备制造、持续研发上具备不可比拟的优势,完全驾驭了COREX工艺的设计以及生产操作,并对该技术进行了很好的消化、吸收,发展成为具有中国特色的欧冶炉熔融还原炼铁工艺,展现了中国熔融还原炼铁技术的巨大进步。
1.2FINEX 熔融还原炼铁工艺
FINEX工艺是韩国浦项制铁开发的创新型熔融还原炼铁工艺,它可直接采用0~8mm铁矿粉(最多可使用30%的磁铁矿)和非焦煤作为原燃料,因此原燃料成本低,拓宽了原燃料使用范围,并因省掉烧结和焦化工序,能够大幅减少污染而实现清洁生产。FINEX工艺流程如图2所示。
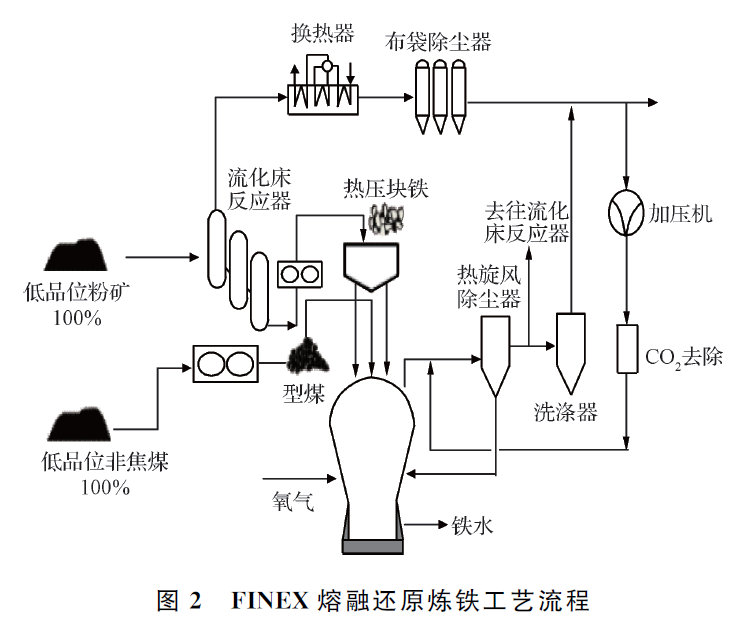
浦项公司第1套商业化FINEX生产线,年生产能力为150万t铁水的FINEX工厂于2004年开工建设,2007年投产,年生产能力为200万t铁水的FINEX工厂于2014年投产,实现了FINEX工艺生产规模大型化,技术装备日益成熟。浦项公司在FINEX工艺的研发上值得学习,成立了专门的FINEX工艺研发机构和推广机构,专业技术人员和技术推广人员齐备,投入了大量的人力、物力、财力来发展和推广FINEX工艺。FINEX工艺创造性的将流化床还原铁矿粉工艺和熔融气化炉结合在一起,并推动了流化床还原铁矿粉工艺技术进步。在已有技术的基础上,为满足FINEX工艺要求,进行了创新性的技术改进。近年来,浦项公司在FINEX工艺上的技术进步主要体现在如下几个方面:
(1)流化床工艺设备大型化。FINEX工艺的核心技术是流化床还原技术,即通过流化床还原装置,使熔融气化炉产生的还原气体对粉矿进行预还原,目前浦项公司的流化床处理铁矿粉的能力已经能够满足年产200万t熔融还原铁水的需要,满足对设定的流化床还原率的要求,还原率达到60%,浦项公司在流化床工艺的大型化上技术进步巨大。
(2)流化床系统工艺布置优化。流化床系统的上料方式由原来的机械设备垂直上料改成气力输送上料;流化床反应器由四级改成三级;经过优化设计后,流化床反应器系统整体高度由121降低到77 m,简化了工艺环节,大幅降低工程投资。
(3)能源高效利用。流化床煤气近年来已实现了余热回收蒸汽,吨铁回收蒸汽210 kg,流化床煤气采用干法除尘,外供煤气热值提高,吨铁发电量增加。
(4)与高炉炼铁流程协同生产效益明显。高炉流程中焦化工序产生的干熄焦灰及运转焦灰,高炉筛下小粒度焦(≤10 mm)、返矿均可由FINEX配吃、消化,在改善高炉原燃料条件的前提下,充分回收高炉流程废弃料,减少外排废弃物,环境效益和经济效益明显。
通过对浦项公司FINEX工艺的研发过程进行了解,发现浦项公司进入熔融还原炼铁工艺领域比较早,技术研发与生产紧密结合,是典型的产学研深度融合、一体化的公司,研发工作有组织,有目标,具备一套完整的技术创新体系,因此,FINEX工艺技术成熟迅速,自主推广能力强。
1.3HIsmelt熔融还原炼铁工艺
HIsmelt工艺是由力拓、纽科、三菱、首钢合资开发的熔融还原炼铁工艺,原试验基地位于西澳大利亚奎纳纳工业区,年设计能力80万t,产品为生铁。2005年建成开始试生产。HIsmelt工艺流程如图3所示。
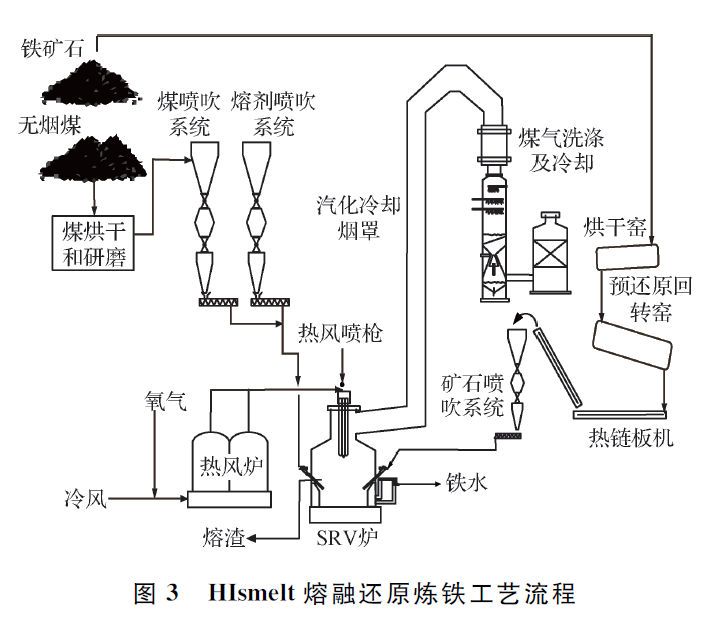
2012年山东墨龙公司与力拓公司签订协议,将澳大利亚奎那那的HIsmelt 工业装置搬迁至中国,经过改造后于2016年年底投产运行,目前主要生产指标已明显优于力拓HIsmelt工厂。改造后的矿粉预热系统采用两级回转窑预热工艺,烘干回转窑的出料温度为80~100 ℃;预还原回转窑采用50%煤+50%SRV炉煤气加热铁矿粉,温度达到750 ℃以上,物料的还原度达到15%以上。该工艺的引进、消化,符合中国的钢铁工业结构调整,炼铁工艺升级换代,淘汰落后技术,实现钢铁工业可持续发展产业政策的战略需求,HIsmelt工艺具有原料的灵活性、操作的灵活性、投资低、铁水质量好等特点。
HIsmelt工艺在中国的发展时间比较短,研发和改进需要一定时间的技术积累。根据目前跟踪生产情况的了解,有如下几个方面可以进行提升优化:
(1)将SRV炉煤气湿法除尘改造为干法除尘。中国的煤气干法除尘技术在世界上具有领先优势,而国外的煤气清洗方式多采用湿法除尘,COREX工艺和FINEX工艺均存在此类问题,欧冶炉干法除尘的成功应用,有效提高了能源利用率,SRV炉煤气初始温度为1 600 ℃,是这几种熔融还原炼铁工艺中煤气温度最高的,完全可以设计多级热量回收,在充分回收能源后,采用干法除尘工艺进行煤气清洗。
(2)研发采用吹氧冶炼。HIsmelt工艺的SRV炉采用富氧热风(氧气体积分数为39%)助燃,热风温度为1 100~1 200 ℃,需要配套建设热风炉,增加了不必要的投资和二次能源消耗,同时,由于采用空气助燃,空气中的氮气降低了SRV炉煤气的热值。借鉴COREX和FINEX采用氧气冶炼的技术,研发氧气冶炼技术,是HIsmelt工艺技术进步的方向。
(3)研发一步法碳-氢熔融还原炼铁工艺。山东墨龙的预还原回转窑工艺铁矿石的还原度比较低,鉴于还原度不佳,同时在国内环保要求趋严,限煤日益严格的条件下,不具备进一步发展煤基预还原回转窑的政策条件,建议取消预还原回转窑,只设计矿石烘干窑,燃料采用SRV炉煤气,降低SO2污染物排放。同时,SRV炉采用底吹氢气的工艺,研发碳-氢熔融还原炼铁工艺,提高矿粉还原效率,降低工序能耗,降低燃煤消耗,实现低碳、低排放炼铁,成为真正的一步法熔融还原炼铁工艺。
(4)关键设备国产化。HIsmelt工艺是真正接近于一步法的熔融还原炼铁工艺,没有燃料和矿粉的造块工艺,主要工艺系统包括:矿粉预热及烘干、热矿喷吹、粒煤制备及喷吹、熔剂喷吹、SRV炉本体、热风炉、出铁场、鼓风、煤气清洗等系统。由此可见,除了SRV炉本体和热矿喷吹外,其他均为高炉长流程工艺的常规系统,国内均有成熟的设计和生产运行经验。SRV炉本体和热矿喷吹主要工艺设备有热风喷枪、矿煤喷枪、热矿螺旋输送机、热矿链板输送机,关键设备少,设备结构相对简单,随着生产实践的积累,如何使上述设备延长服役寿命,提高使用效果,更加简洁的操作和更换,是引进HIsmelt工艺后需要消化和创新的必经之路,依靠中国强大的工业体系,上述设备完全可以实现自主研发,更好地为SRV炉体服务。
2.1熔融还原炼铁工艺参数整理
通过对上面对3种主要熔融还原炼铁工艺的介绍,对3种工艺的主要工艺参数和工艺设备进行简要整理,结果见表1。
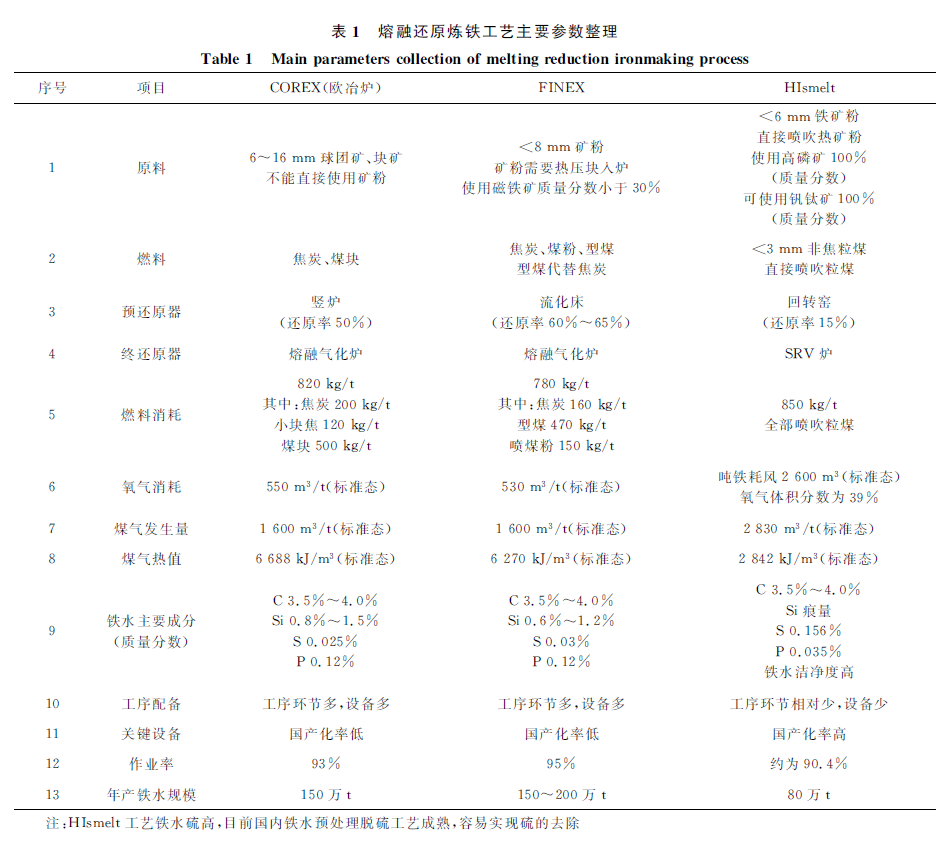
完整的对熔融还原炼铁技术的经济性对比分析包括5个方面:工艺成熟性、生产成本、投资费用、环境友好性和原燃料要求。国内很多专家均对熔融还原炼铁工艺从上述5个方面进行了很好的总结和分析,本文不再赘述。下面阐述近年来对熔融还原炼铁工艺技术进行追踪的一些个人观点。
2.2对于如何选择熔融还原炼铁工艺的一些观点
随着欧冶炉的技术进步以及HIsmelt工艺在山东墨龙的建成投产,中国已经成为熔融还原炼铁工艺发展的主要市场,中国炼铁科技工作者已经成为熔融还原炼铁技术发展的主力军,根据最近几年对熔融还原炼铁技术的追踪,建议有意向选择熔融还原炼铁技术的企业遵循如下几个原则:
(1)熔融还原炼铁短流程工艺在煤炭资源丰富而且廉价的地区有良好的发展前景。中国的新疆和内蒙地区煤炭资源丰富而且具有价格优势,欧冶炉在新疆八一钢铁公司的良好运行充分证明了燃料资源优势的重要性。
(2)解决部分劣质炼铁矿石的冶炼难题。例如,中国以及世界上存在大量高磷铁矿石,如何盘活利用高磷铁矿资源,使其转变为市场效益,一直是冶金界的难题,HIsmelt工艺为高磷铁矿石的冶炼提供了一种可供选择的工艺路线,由于SRV炉内存在氧化性气氛,适宜磷的脱除,铁水中的磷含量很低,脱磷效果很好,钒钛磁铁矿的冶炼难题也可以由HIsmelt工艺解决,用HIsmelt熔融还原技术冶炼高磷铁矿和钛铁矿都分别取得良好的效果。HIsmelt工艺铁水洁净度高,适合高质量产品需要。
(3)独立电炉企业宜选择HIsmelt工艺进行协同生产,HIsmelt工艺能够脱除铁水中的有害元素,相比于长流程的高炉铁水,熔融还原工艺的COREX铁水、FINEX铁水以及目前电炉的主原料废钢,HIsmelt工艺铁水更洁净,适宜电炉冶炼工艺,能够提高电炉钢水质量,解决电炉采用100%废钢冶炼,影响钢水洁净度的难题,满足高质量产品的需求。国外独立电炉厂生产高质量钢水的工艺路线通常选择直接还原铁工艺,用DRI(直接还原)代替废钢,但DRI相对铁水来说依旧属于冷料,限于中国的电力资源,电炉热装铁水是比较经济的工艺路线。鉴于目前HIsmelt工艺还不具备大型化生产的实践,60~80万t的年产铁水量,产能规模不大,配加一定比例废钢后,恰好是大型电炉厂比较适宜的铁原料结构,同时SRV炉还能为电炉钢厂提供SRV炉煤气,满足轧钢工序的需求,解决独立电炉企业的廉价燃气资源问题。此外,在中国,独立电炉企业如果建设直接还原铁装置,还需要外部环境创造条件,一方面受制于资源情况,DRI需要高品位铁精粉,但目前中国生产的直接还原铁因原料含铁较低,产品质量难以满足电炉生产洁净钢、优质钢的要求,因此铁精粉需要进一步精选,高品位铁精粉属于稀缺资源。另一方面,中国天然气资源匮乏,需要发展煤制气工艺来生产直接还原铁工艺需要的高品质还原气,而这需要国家政策引导和地方政府的支持。目前国内DRI资源匮乏,独立电炉企业为冶炼高品质钢水,需要进口DRI,价格高昂。
(4)COREX工艺和FINEX工艺宜与传统高炉炼铁工艺协同生产,协同效果显著。COREX和FINEX工艺已经实现年产150万和200万t规模的商业化生产,与传统高炉炼铁工艺协同生产,可满足大型钢铁企业的生产规模要求,又能实现很好的经济效益和社会效益。韩国浦项公司的生产实践,宝武集团八一钢铁公司的生产实践均已经证明了协同生产具有很好的生产效益。COREX和FINEX工艺具有占地少,劳动定员少,原燃料质量要求低,生产成本低、工艺流程少、低排放、低污染等特点,这与长流程高炉工艺的现状正好形成互补。另外,从产品角度分析,因为COREX和FINEX工艺铁水硅含量高,在铁水罐内容易出现粘罐现象,给生产组织造成很大困难,同时铁水硅高增加炼钢工序的生产成本。熔融还原高硅铁水与高炉低硅铁水混兑后,避免了铁水粘罐现象,同时铁水可以直接供给炼钢工序,由此可见,与高炉长流程工艺的协同生产,解决了目前COREX工艺和FINEX工艺铁水硅高带来的生产难题,形成了很好的互补。
总结中国引进COREX工艺和HIsmelt工艺的经验和技术创新,说明中国在熔融还原炼铁工艺的技术积累上已经取得了长足进步,在此基础上,结合FINEX工艺的生产实践和技术创新,从中国国情出发,因地制宜、合理的选择熔融还原炼铁工艺路线,是实现低碳炼铁的一条重要途径,随着中国炼铁技术的不断进步,中国炼铁工作者在消化、吸收引进的熔融还原炼铁技术的基础上,必然会推动熔融还原炼铁技术向更深层次发展。
$ST墨龙(SZ002490)$$山东墨龙(HK|00568)$
本文作者可以追加内容哦 !