在快节奏的生产环境中,设备停机时间无疑是每个企业都头疼的问题。它不仅影响生产效率,还可能造成巨大的经济损失。那么,有没有一种神奇的方法能够一键减少设备停机时间呢?答案就是--TPM(全面生产维护)!具体步骤如深圳天行健企业管理咨询公司下文所述:
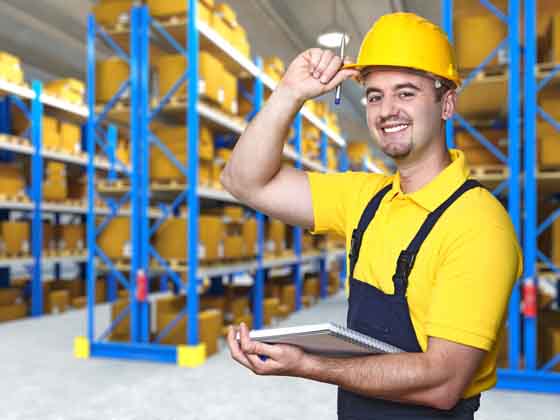
一、预防性维护
1. 制定详细的维护计划
- 根据设备的特点、运行状况和厂家建议,制定定期的检查、保养和维修计划。例如,对于一台关键的生产设备,规定每三个月进行一次全面的保养,包括清洁、润滑、紧固和部件检查。
- 一家汽车制造工厂为其冲压设备制定了预防性维护计划,提前更换易损部件,有效避免了因部件突发故障导致的停机。
2. 基于状态的监测
- 利用传感器和监测技术实时收集设备的运行数据,如温度、压力、振动等,通过数据分析预测可能的故障,并提前进行维护。比如,通过对一台数控机床的振动监测,发现其主轴存在异常振动,及时进行维修,防止了故障的进一步恶化。
二、员工培训与参与
1. 技能提升培训
- 为操作人员和维修人员提供设备操作和维护方面的培训,使他们能够正确使用设备、及时发现异常并进行简单的故障排除。例如,组织员工参加设备操作和维护的培训班,学习设备的工作原理和常见故障处理方法。
- 某电子厂对员工进行了贴片设备的操作培训,员工能够在设备出现小故障时迅速采取正确的应对措施,减少了停机时间。
2. 自主维护
- 鼓励操作人员参与设备的日常清洁、检查和保养工作,增强他们对设备的责任感和熟悉度。比如,操作人员在工作前对设备进行简单的检查,及时发现并报告潜在问题。
三、快速换模(SMED)
1. 优化换模流程
- 对设备的换模过程进行分析,消除不必要的步骤和动作,缩短换模时间。例如,通过重新布局模具存放区域和改进工具的取用方式,将换模时间从原来的 2 小时缩短至 1 小时。
- 一家注塑工厂实施了 SMED 方法,对模具更换流程进行了重新设计和标准化,大幅减少了换模导致的停机时间。
2. 标准化作业
- 制定详细的换模作业标准,确保每次换模都按照相同的步骤和标准进行,提高效率和稳定性。
四、备件管理
1. 合理储备备件
- 根据设备的故障历史和关键部件的寿命,确定备件的种类和数量,确保在设备出现故障时能够及时更换。比如,对于经常损坏的电机,储备一定数量的备用电机。
- 一家化工厂对关键设备的备件进行了科学的预测和储备,当设备突发故障时,能够迅速更换备件,恢复生产。
2. 备件库存优化
- 定期评估备件库存,避免积压和短缺,提高备件的周转率。
五、故障根源分析与解决
1. 深入分析故障原因
- 当设备出现故障停机时,不仅仅是修复故障部件,更要深入分析故障的根本原因,采取措施防止再次发生。例如,通过鱼骨图等工具对故障进行全面分析,找出导致故障的多个因素,并逐一解决。
- 某纺织厂的一台纺纱机频繁出现断纱故障,经过深入分析,发现是由于张力控制装置不稳定,通过改进装置,彻底解决了断纱问题,减少了停机次数。
2. 持续改进机制
- 建立故障数据库,对每次故障的情况、原因和解决措施进行记录和分析,为后续的维护和改进提供参考。
综上所述,TPM通过综合运用以上多种方法,有效地减少了设备停机时间,提高了设备的可靠性和生产效率。
本文作者可以追加内容哦 !